Table of Contents
Introduction
The Global Welding Equipment Market is projected to expand from USD 16.8 billion in 2023 to an estimated USD 34.0 billion by 2033, exhibiting a Compound Annual Growth Rate (CAGR) of 7.3% throughout the forecast period from 2024 to 2033.
Welding equipment encompasses devices and accessories used to join metal parts through various techniques, including arc, resistance, laser, and electron beam welding. These tools range from basic handheld devices to complex automated systems. The welding equipment market refers to the commercial landscape in which these technologies are developed, manufactured, and sold, impacting sectors such as construction, automotive, and manufacturing.
Growth in this market is primarily driven by the increasing demand from these industries for more efficient and advanced welding solutions, spurred by infrastructural developments and technological advancements. Additionally, a rise in the adoption of automated welding solutions in high production environments offers significant growth opportunities. This trend is further supported by the growing emphasis on precision and speed in manufacturing processes, leading to heightened demand for sophisticated welding technologies that ensure high-quality results.
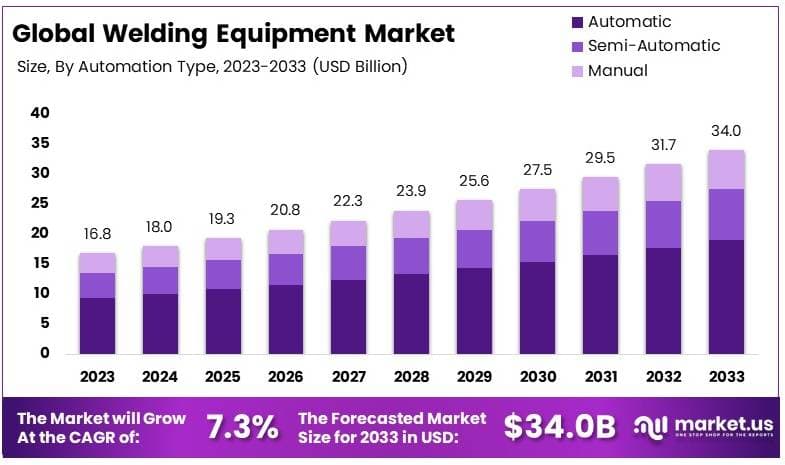
Fundamental Insights
- The Welding Equipment Market was valued at USD 16.8 billion in 2023 and is projected to grow to USD 34.0 billion by 2033, achieving a CAGR of 7.3%.
- Automatic welding machines accounted for 55.8% of the market in 2023, favored for their precision and efficiency in industrial applications.
- Arc welding was the leading technology in 2023, capturing 69.4% of the market, indicative of its extensive application across various industries.
- The automotive industry comprised 23.8% of the market in 2023, underscoring its dependency on advanced welding solutions for manufacturing.
- The Asia Pacific region led the market with a 35.6% share in 2023, driven by significant industrial advancements in China and India.
Report Scope
Report Features | Description |
---|---|
Market Value (2023) | USD 16.8 Billion |
Forecast Revenue (2033) | USD 34.0 Billion |
CAGR (2024-2033) | 7.3% |
Segments Covered | By Automation Type (Automatic, Semi-Automatic, Manual), By Technology (Arc Welding, Laser Beam Welding, Resistance Welding, Oxy-Fuel Welding, Other Technologies), By End-Use Industry (Building and Construction, Automotive, Oil & Gas, Energy, Aerospace, Other End-Use Industries) |
Competitive Landscape | ACRO Automation Systems Inc, Lincoln Electric, AIR LIQUIDE, voestalpine Böhler Welding Group GmbH, Carl Cloos Schweisstechnik GmbH, OTC DAIHEN Inc., Panasonic Industry Co. Ltd., Polysoude S.A.S., Coherent Inc., Illinois Tool Works Inc., Other Key Players |
Regional Analysis
Asia-Pacific Leads Welding Equipment Market with Largest Market Share of 35.6%
In 2023, the Asia-Pacific region dominated the global welding equipment market, holding the largest market share of 35.6%. The market in this region was valued at USD 5.98 billion, underscoring its pivotal role in the industry’s growth dynamics. This significant market share is attributed to extensive industrial activities, particularly in automotive, construction, and heavy machinery sectors across countries like China, India, and Japan.
These nations have witnessed substantial investments in infrastructure development and manufacturing capacities, fueling the demand for advanced welding technologies and equipment. The robust growth in these sectors is likely to continue, driven by increasing urbanization and industrialization, along with supportive government policies aimed at enhancing manufacturing capabilities. As a result, Asia-Pacific is not only the current leader but also poised for continued dominance in the welding equipment market, propelled by ongoing technological advancements and increasing adoption of automation and robotics in welding processes.

Emerging Trends
- Hybrid Welding: Combining laser welding with traditional methods like GTAW (gas tungsten arc welding) or MIG welding is gaining popularity. This combination offers precision and control while minimizing the drawbacks of each individual method, making it suitable for a variety of materials and thicknesses.
- Automation and Robotics: The integration of Industry 4.0 technologies is transforming welding through increased use of automation and robotics. This shift not only enhances efficiency and quality but also improves safety by reducing human exposure to hazardous conditions.
- Additive Manufacturing (3D Printing): 3D printing is being increasingly used in welding to create complex structures and perform in-place repairs, which can significantly reduce downtime and costs, particularly in industries like aerospace and healthcare.
- Sustainable Welding Practices: As environmental concerns grow, there is a notable shift towards sustainable welding techniques. These include using renewable energy sources, non-toxic materials, and energy-efficient systems to reduce the environmental impact of welding operations.
- Advanced Materials: The use of innovative materials such as high-strength steels and lightweight alloys is on the rise. These materials require specialized welding techniques and offer improved performance, which is crucial for industries like aerospace and automotive.
Top Use Cases
- Manufacturing Industry: Welding is fundamental in manufacturing, where it is used in the production of everything from cars to construction equipment. The versatility and efficiency of modern welding techniques are vital for meeting the diverse demands of this sector.
- Construction: Robust welding solutions are essential for constructing infrastructure such as buildings and bridges, where strength and durability are paramount.
- Automotive Assembly: In automotive manufacturing, welding is used to assemble everything from chassis to engine components. Advances in welding technologies, like robotic and laser welding, have significantly improved the speed and precision of these processes.
- Aerospace Applications: Welding technologies capable of handling lightweight and advanced materials are crucial in aerospace for the production and maintenance of aircraft and spacecraft components.
- Shipbuilding: Welding is a key operation in shipbuilding, where it is used to assemble large metal sections of ships. The industry benefits from both traditional and advanced welding techniques to ensure structural integrity and safety.
Major Challenges
- Skills Shortage: There is a significant demand for skilled welders who are proficient with the latest technologies. The complexity of modern welding techniques requires continuous training and updating of skills.
- Quality Control: Maintaining consistent weld quality is challenging, especially with complex and automated systems. This can impact the overall integrity and safety of the welded structures.
- Health and Safety Risks: Welding processes can expose workers to harmful fumes and intense heat. Despite advancements in protective gear, maintaining workplace safety remains a crucial challenge.
- Technological Integration: Integrating new technologies such as robotics and AI with existing welding setups can be complex and costly, requiring significant investment in equipment and training.
- Material Compatibility: As new materials become more common, finding compatible welding techniques becomes more challenging. Each material may require different welding methods to ensure strong and durable joints
Top Opportunities
- Expansion into Renewable Energy Sectors: The growing renewable energy sector requires extensive use of welding for constructing solar frames, wind turbines, and other infrastructures. This sector offers significant growth opportunities for welding equipment manufacturers.
- Advancements in Automation: Investing in automated welding technologies offers the potential for increased efficiency and lower labor costs, particularly in high-volume manufacturing environments.
- Emerging Markets: Developing regions are witnessing rapid industrialization, which creates new markets for welding equipment. These regions present opportunities for expansion and establishing new customer bases.
- Customization and Flexibility: There is increasing demand for welding systems that offer customization and flexibility to handle various materials and tasks. Equipment that can be easily adapted for different applications has a competitive edge.
- Aftermarket Services and Training: Providing comprehensive service and training programs can open additional revenue streams for welding equipment manufacturers. These services are essential for customers to maximize the utility and lifespan of their equipment.
Key Player Analysis
- Lincoln Electric: Known for its leadership in the welding industry, Lincoln Electric provides a wide array of welding products, including arc welding equipment, plasma and oxyfuel cutting equipment, and robotic welding systems. The company focuses heavily on innovation and technology, leading advancements in automated and robotic welding solutions. Its comprehensive approach maintains a strong global presence and caters to sectors like automotive, construction, and heavy machinery.
- AIR LIQUIDE: Specializing in gas-based welding solutions, AIR LIQUIDE has a significant international footprint. The company’s expertise in welding gases and services across various industries, including energy, manufacturing, and healthcare, has positioned it as a leader. By leveraging its gas technology, AIR LIQUIDE provides efficient and sustainable welding solutions, reflecting its strategic market position.
- Illinois Tool Works Inc. (ITW): ITW offers an extensive portfolio of welding products under its brand, including Miller Electric. The company excels in providing innovative and user-friendly welding equipment, catering to both small and large industrial clients. ITW’s focus on high-efficiency welding solutions helps maintain its status as a market leader.
- voestalpine Böhler Welding Group GmbH: Part of the voestalpine Group, this company is recognized for its specialty in producing high-quality welding consumables and equipment. The company operates in key sectors like oil and gas, power generation, and automotive, offering tailored solutions that meet the rigorous demands of these industries. Their commitment to quality and innovation supports their strong market presence.
- Panasonic Industry Co. Ltd.: This company is a significant player in the welding sector, known for integrating cutting-edge technology into its welding products. Panasonic Industry focuses on delivering solutions that enhance productivity and quality in welding, with a strong emphasis on the development of automated welding technologies and systems that incorporate advanced features like real-time control and monitoring
Recent Developments
- In 2023, Techniweld USA acquired Welding Material Sales, significantly enhancing its market presence with the addition of the popular Blue Demon product line. This strategic move broadens Techniweld’s distribution capabilities across seven locations and enriches its offerings in specialty welding supplies and filler metals.
- In 2024, Novarc Technologies Inc. introduced NovEye Autonomy Gen 2. This advanced system leverages real-time vision processing to refine welding quality through continuous data-driven improvements, marking a significant step in the automation of pipe welding.
- In 2023, Miller Electric Mfg. LLC launched the Millermatic 142 MIG welder, a compact device that supports both professional and hobbyist welders with its ease of use and consistent quality, reinforcing Miller’s commitment to excellence in every project.
- In 2023, Kemppi introduced the Master M 205 and Master M 323 models, portable welding machines designed for versatile uses from industrial applications to hobby projects. Their compact design and advanced features were developed in Finland, emphasizing ease of use and high-performance standards.
- In 2024, Rinco Ultrasonics announced the release of its new Ultrasonic Servo Driven Splicer at The Battery Show, expanding its offerings in ultrasonic metal welding with a system designed for high-performance wire splicing.
Conclusion
The welding equipment market is poised for significant growth over the next decade, driven by technological advancements and increasing industrial demand. The expansion is particularly fueled by the rise of automation and the integration of innovative welding techniques, catering to industries like automotive, construction, and aerospace. Furthermore, the growing emphasis on sustainable practices and the adoption of advanced materials are reshaping welding processes, thereby broadening the scope and applicability of welding technologies. As this market continues to evolve, it presents numerous opportunities for enhancement in efficiency and productivity, along with challenges related to skill requirements and quality assurance. Overall, the future of welding equipment looks promising, with a strong trajectory for continued development and expansion across various sectors.
Discuss Your Needs With Our Analyst
Please share your requirements with more details so our analyst can check if they can solve your problem(s)
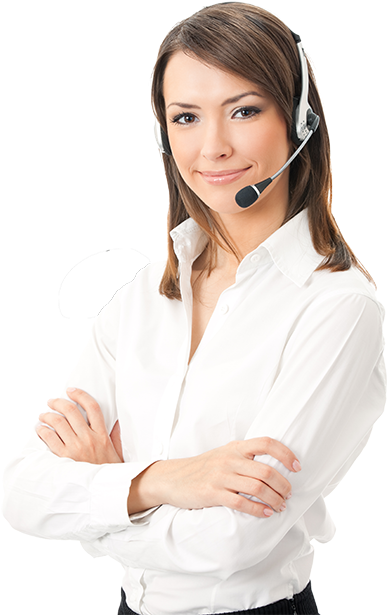