Table of Contents
Introduction
The global Powder Metallurgy Market is set for impressive growth, expected to rise from USD 11 billion in 2023 to approximately USD 26 billion by 2033, with a CAGR of 8.8%. This growth is driven by technological advancements like additive manufacturing (AM) and powder metal hot isostatic pressing (PM HIP), which enhance the production of complex and precision components crucial in the aerospace, defense, and healthcare sectors.
However, the market faces challenges such as the high costs associated with advanced metallurgy technologies and the rigorous performance demands from various industries. Additionally, geopolitical issues and disruptions in the supply chain pose risks that could affect material supply and market stability.
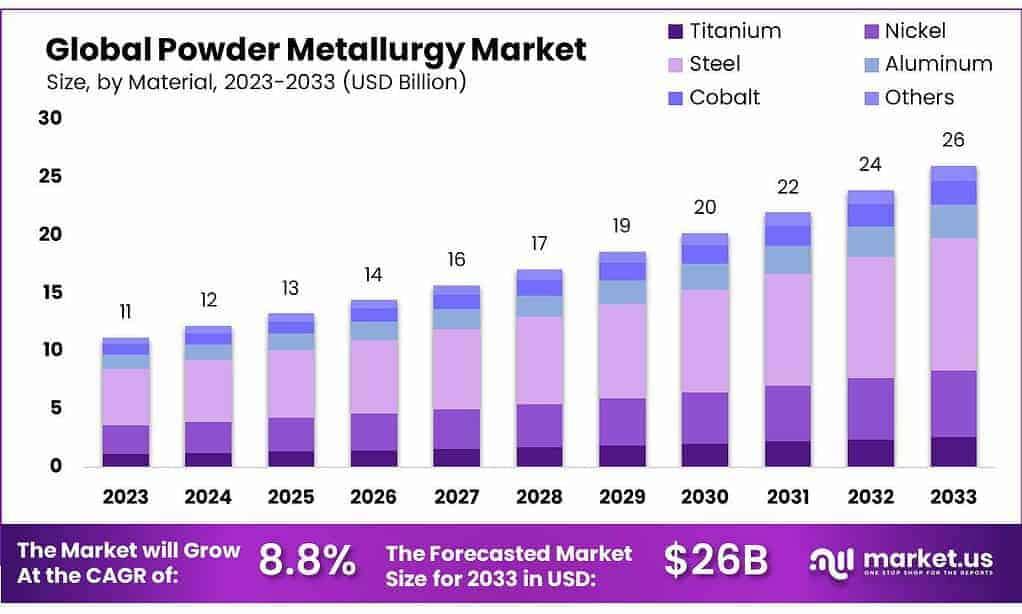
Recent developments underscore the industry’s commitment to sustainability and efficiency. Key players focus on research and development to improve metal powder properties and broaden their application scope.
Strategic acquisitions also shape the market, aiming at expanding reach and enhancing product portfolios. Notably, in 2023, 6K Additive acquired Global Metal Powder, aiming to boost the production of refractory powders and foster the development of sustainable products.
AT&M has been expanding its capabilities in the powder metallurgy sector. A notable development occurred when AT&M formed a joint venture named Advanced Technology (Bazhou) Special Powder Co., Ltd.
This venture focuses on the production of various specialist powders, including metal injection Moulding powders and powder metallurgy powders, aiming to reach a production capacity of 10,000 tons per annum.
Key Takeaways
- Powder Metallurgy Market size is expected to be worth around USD 26 billion by 2033, from USD 11 billion in 2023, growing at a CAGR of 8.8%.
- Steel held a dominant market position in the powder metallurgy market, capturing more than a 43.5% share.
- Additive Manufacturing held a dominant market position in the powder metallurgy market, capturing more than a 41.3% share.
- Aerospace & Defense held a dominant market position in the powder metallurgy market, capturing more than a 33.4% share.
- OEMs (Original Equipment Manufacturers) held a dominant market position in the powder metallurgy market, capturing more than a 68.5% share.
- Asia Pacific (APAC) leads this market with a 36% share, valued at approximately USD 4.04 billion.
Powder Metallurgy Statistics
Investments Surge in Powder Metallurgy
- Already in use at the factories of Porsche, Siemens, PON.bike, and GKN Powder Metallurgy, Munich’s Workerbase welcomes €10 million in a Series A funding round.
- AM 4 AM announced that the €1.3 million investment will fund the expansion of its facilities and enhance its production and product development capabilities.
- m4p material Solutions GmbH, with operations in both Austria and Germany, has announced it has received a €3 million investment from Finindus NV and Berkau Beteiligungs GmbH.
- An EU project coordinated by the European Powder Metallurgy Association (EPMA) has been granted €7.3 million. The funding, divided between thirteen partners under the REPTiS project, is intended to support the responsible extraction and processing of titanium and other primary raw materials for sourcing EU industrial value chains and strategic sectors.
- Altmin Private Ltd., a leading manufacturer of cathode active material for lithium-ion batteries in India, has announced plans for a US$ 100 million investment over the next five years. A well-known Indian family office, known for its proficiency in iron phosphate and other precursor manufacturing in India, provided growth capital to the company.
Funding Boosts Powder Metallurgy Growth
- C3 Med-Tech has secured ₹2 crore in VC funding from Industrial Metal Powders. The funding will be utilized to launch its telemedicine and AI-enabled portable equipment for eye checkups and disease detection.
- Ahmedabad-based health tech startup C3 Med-Tech has raised Rs 2 crore in funding from Industrial Metal Powders.
- Metal recycler and additive manufacturing material producer Continuum, Los Gatos, California, announced it has raised a total of $36 million in funding, led by Houston-based Ara Partners.
- Specialist engineer Dowlais (DWL) has been dragged into a £450mn operating loss by a major goodwill impairment. The group – which was spun off from Melrose Industries (MRO) last year – has reported a £449mn impairment charge relating to its powder metallurgy division, following a review of its medium-term prospects. The group was further hampered by £120mn of restructuring costs in the automotive business.
- 6K Inc., located in North Andover, Massachusetts, USA, announced that it has raised $82 million as part of its Series E funding round. The capital is expected to enable the company to scale up production for battery cathode active materials (CAM) and expansion for producing Additive Manufacturing metal powders.
Emerging Trends
- Sustainability and Environmental Considerations: The industry is increasingly focusing on sustainable practices. Innovations include recycling used metal powders and optimizing manufacturing processes to minimize waste and energy consumption. Companies are exploring environmentally friendly materials and processes to meet regulatory standards and consumer demands for greener products.
- Advanced Additive Manufacturing (AM) Technologies: Additive manufacturing is evolving, with new technologies like powder bed fusion and direct metal laser sintering driving the growth. These methods allow for more complex geometries and the efficient production of components, particularly for aerospace, medical, and automotive applications.
- Development of New Material Composites: The incorporation of high-entropy alloys and metal matrix composites in powder metallurgy offers enhanced properties such as improved strength, durability, and thermal performance. These materials are particularly beneficial in high-performance applications across various industries.
- Integration with Digital Technologies: The integration of Industry 4.0 technologies, such as IoT and AI, into powder metallurgy processes is enhancing production efficiency and product quality. Digital technologies help in monitoring the manufacturing process and in predictive maintenance, leading to lower operational costs and improved production cycles.
- Tailored Microstructural Properties: There is an increasing focus on developing powders and processes that can produce parts with specific microstructural properties. Techniques such as fast sintering and unconventional sintering processes are being developed to control the microstructure of metals, enhancing their mechanical and physical properties for specialized applications.
Use Cases
- Automotive Industry: Powder metallurgy is extensively used in the automotive sector, making up a significant portion of the market. This method is ideal for manufacturing complex and lightweight components that contribute to overall vehicle lightness, which is crucial for improving fuel efficiency and reducing emissions in modern vehicles.
- Electronics and Appliances: In the production of household appliances and electronic components, powder metallurgy plays a crucial role due to its ability to produce high-precision parts like gears, levers, and other mechanisms found in devices such as washing machines and lighting controls.
- Aerospace Applications: The aerospace industry benefits from powder metallurgy mainly through the manufacture of high-strength, lightweight parts that withstand extreme operational environments. This includes critical components like turbine blades made from superalloys.
- Medical Devices: Powder metallurgy is used to create components for medical implants and surgical tools. This technology allows for the production of high-volume, precise parts that meet the stringent standards required in medical applications, often at a lower cost and with less waste compared to traditional manufacturing methods.
- Industrial Machinery: In sectors such as construction and agriculture, powder metallurgy contributes to the manufacturing of durable components used in heavy machinery and equipment. This includes parts for engines and hydraulic systems that benefit from the wear resistance and strength provided by powder metallurgically processed materials.
Major Challenges
- Adapting to Technological Advances: As the demand for advanced materials grows, the powder metallurgy sector must evolve with the latest technological innovations. This includes embracing new manufacturing techniques like additive manufacturing, which necessitates continuous improvements in material properties and production methodologies to meet industry standards.
- Complexities in Supply Chain Management: The industry faces intricate challenges in managing supply chains, particularly in procuring and stabilizing the flow of raw materials. The demand for specific material properties, coupled with the drive towards sustainable practices, adds layers of complexity to sourcing and logistics.
- Navigating Environmental and Regulatory Pressures: Environmental sustainability is increasingly shaping the powder metallurgy sector, with pressures to minimize emissions and waste while boosting recycling efforts. Striking a balance between adhering to stringent environmental regulations and maintaining cost-effective production is a significant challenge.
- Market Volatility and Economic Impacts: Economic shifts significantly influence the powder metallurgy industry, affecting investment and development. Notably, transformations within the automotive sector, such as the transition towards electric vehicles, require the industry to innovate and adapt to new material needs and applications.
- Bridging the Skills Gap: There is an urgent need for skilled professionals capable of handling emerging technologies and driving innovation in the powder metallurgy field. The industry must invest in training and development to close the skills gap and support growth and technological advancement.
Market Growth Opportunities
- Expansion into New Markets: There’s potential growth in various sectors, including energy, aerospace, medical, dental, and defense, where the demand for precision and lightweight components is increasing. The aerospace and defense sectors, for instance, are particularly promising due to their need for complex geometric structures and new materials.
- Advancements in Additive Manufacturing: Additive manufacturing (AM) is set to register significant growth, especially in creating prototypes and complex components across key industries like aerospace, automotive, and healthcare. This growth is driven by AM’s ability to reduce turnaround times, minimize errors, and lower production costs.
- Development of New Materials: Innovations in material science, such as the creation of lean-alloy materials and high-wear-resistance alloys, are creating new opportunities within the industry. These materials are designed to meet current and future sustainability demands and offer enhanced performance characteristics.
- Increased Application in Electric Vehicles: As the automotive industry shifts from internal combustion engines to electric vehicles, there is a growing demand for magnetic materials that are used in electric motors. This shift highlights the role of powder metallurgy in producing components like soft magnetic composites, which are crucial for advanced motor designs.
- Sustainability and Circular Economy Practices: The industry’s focus on sustainability is leading to increased recycling and the use of scrap materials in production processes. This aligns with global efforts to reduce CO2 emissions and improve environmental impact, presenting a significant opportunity for growth through green manufacturing practices.
Key Players Analysis
- Advanced Technology & Materials Co., Ltd. (AT&M) specializes in the research, development, and manufacture of new metallic materials, including a focus on powder metallurgy products. Established by the China Iron & Steel Research Institute Group and publicly listed in 2000, AT&M serves industries like aerospace, IT, and energy with innovative material solutions.
- ATI Powder Metals, part of the ATI group, excels in powder metallurgy, offering a comprehensive range of services from atomization through hot isostatic pressing (HIP). They are notable for their fully integrated manufacturing of nickel-base superalloys, operating large-scale vacuum induction melt atomizers.
- Catalus Corporation, originally known as SMC Powder Metallurgy and a part of St. Marys Carbon, has been innovating in the powder metallurgy sector since the 1950s. Specializing in high-strength, wear-resistant, corrosion-resistant, and magnetic powder metal parts, Catalus serves industries like automotive, aerospace, and medical. They offer a range of custom engineering services and value-added processes such as heat treatment and machining, maintaining high-quality standards as an ISO 9001:2015 certified company.
- CRS Holdings Inc. is recognized as a prominent player in the powder metallurgy market, contributing significantly to advancements in high-performance specialty alloys for various critical applications. These applications span across aerospace, transportation, defense, energy, and medical sectors among others. Their involvement in the market is marked by innovative uses of powder metallurgy to produce lighter, more efficient components, particularly leveraging additive manufacturing techniques to meet high industry demands for precision and durability.
- GKN Powder Metallurgy, a part of Dowlais Group plc, leads in creating advanced powder metal components for the automotive and other industries. Using top-tier powder metallurgy technology, they produce sustainable, high-performance components that push industry standards. They have expanded globally with 27 manufacturing sites, emphasizing innovation in metal products and solutions.
- H.C. Starck Tungsten GmbH, part of the Masan High-Tech Materials Group, specializes in producing high-quality tungsten powders and compounds, with a focus on sustainability and innovation. The company leverages over a century of expertise in powder metallurgy to offer products ranging from tungsten carbides to tungstates, catering to diverse industries including automotive, aerospace, and medical technology.
- Höganäs AB is a leader in metal powder production, developing innovative solutions in powder metallurgy for diverse applications such as automotive components and additive manufacturing. They produce a wide range of metal powders, including iron, stainless steel, and various alloy powders, serving industries with high-performance requirements.
- Horizon Technology specializes in advanced powder metallurgy, creating innovative and efficient solutions for small metal parts manufacturing. Since its inception in 2001, Horizon has focused on developing unique processes and materials that enhance the performance and cost-effectiveness of powder metal components. Their expertise allows them to push the boundaries of traditional manufacturing, making previously impossible designs feasible and improving component qualities such as strength and magnetic properties.
- Horizon Technology specializes in advanced powder metallurgy, creating innovative and efficient solutions for small metal parts manufacturing. Since its inception in 2001, Horizon has focused on developing unique processes and materials that enhance the performance and cost-effectiveness of powder metal components. Their expertise allows them to push the boundaries of traditional manufacturing, making previously impossible designs feasible and improving component qualities such as strength and magnetic properties.
- Liberty Powder Metals, part of Liberty House Group, is expanding its capabilities in the powder metallurgy sector by building a new facility in Teesside, UK. This development is aimed at enhancing their production of specialist metals and materials for additive manufacturing. The focus is on producing highly spherical, free-flowing powder suitable for demanding applications like aerospace and automotive, utilizing advanced atomizing technology.
- JSC POLEMA is a leading manufacturer in the powder metallurgy sector, specializing in the production of chromium, molybdenum, and tungsten products, as well as various metal powders and composite materials. Established in 1961, the company supplies high-performance materials for industries including chemicals, oil and gas, aerospace, and power engineering, demonstrating a strong focus on innovation and quality in their field.
- Melrose Industries PLC, which acquired GKN, demerged its GKN Powder Metallurgy and GKN Automotive into the Dowlais Group in March 2023. This strategic move aimed to focus more on its aerospace sector, marking a shift from its previous model of improving and then selling acquired businesses.
- Miba AG leverages powder metallurgy to manufacture high-precision, high-strength components across various industries including automotive and robotics. Their process notably reduces the CO2 footprint by using recycled steel and emphasizes cost-efficiency and reduced material waste. Miba’s expertise allows them to produce complex part geometries while achieving high material and energy efficiency.
- Molyworks Materials Corporation, now rebranded as Continuum Powders focuses on sustainable metal powder production. They’ve innovated the circular economy for metals, utilizing their Greyhound System to transform metal waste into additive manufacturing grade powder, emphasizing environmental benefits and resource efficiency.
- Perry Tool & Research, Inc. specializes in producing complex, precision powder metal parts using a powder metallurgy process. Since 1962, they have served OEM companies, focusing on gears, bearings, and custom mechanical parts with high precision and quality, maintaining close tolerances and efficient production to meet rigorous industry standards.
- Phoenix Sintered Metals, LLC specializes in powder metallurgy, manufacturing sintered metal components for a variety of industries, including automotive, agriculture, and medical. They focus on engineered solutions that enhance performance and efficiency in their products, leveraging their expertise to support a wide range of market needs.
- Precision Sintered Parts has been a key player in the powder metallurgy industry since 1967, specializing in the production of powdered metal parts. They cater to a broad range of industries including sports equipment, agricultural equipment, and power tools. Known for their expertise in handling diverse configurations, they manufacture high-quality, precision parts with a focus on consistency and cost-efficiency. They are ISO 9001:2015 certified and pride themselves on their commitment to continuous improvement and customer satisfaction.
- Rio Tinto Metal Powders specializes in producing iron and steel powders, primarily for powder metallurgy applications in various industries including automotive, appliance, and gardening tools. Their production facilities utilize iron sourced from low-residual ore, ensuring high purity and consistency in their products. Rio Tinto’s powders are known for their cleanliness and are used globally, adhering to strict quality and environmental standards.
- Rusal operates powder metallurgy facilities in Russia, focusing on producing both coarse and fine aluminum powder and paste. These products serve a variety of sectors, including the construction and metal industries. They emphasize enhancing product ranges and have invested in modern equipment to expand capabilities and meet industry demands.
- Sandvik AB excels in the powder metallurgy sector, specializing in the production of gas-atomized metal powders used for advanced manufacturing technologies like metal injection molding and additive manufacturing. Their products include a wide range of metal powder alloys, and they are recognized for their material expertise spanning over 160 years, combined with significant capabilities in powder atomization technology.
- Showa Denko Materials Co., Ltd., now known as Resonac, has been a major player in the powdered metal industry since 1989. Their U.S. branch is known for providing high-quality and technologically advanced products in North America. They focus on maintaining strict tolerances in all their manufacturing processes and are renowned for innovative designs in powdered metal parts.
- Sumitomo Electric Industries, Ltd. has a long history in powder metallurgy, dating back to 1939, with extensive expertise in manufacturing sintered alloy technology for various applications, including automobile parts and tools. They utilize advanced sintering techniques to produce high-strength components and have significantly contributed to the powder metallurgy field by innovating and expanding their product range over the decades.
Conclusion
Powder metallurgy stands as a key technological frontier in manufacturing, offering substantial growth in sectors like aerospace, automotive, and medical industries. Its ability to innovate through additive manufacturing and sustainable practices positions it well for future advancements and broader industrial applications.
Discuss Your Needs With Our Analyst
Please share your requirements with more details so our analyst can check if they can solve your problem(s)
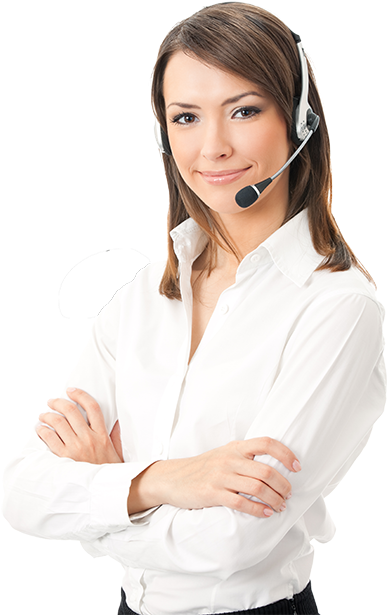