Table of Contents
Introduction
The Global Pneumatic Conveying Systems Market is projected to reach approximately USD 10.5 billion by 2033, up from USD 6.1 billion in 2023, reflecting a compound annual growth rate (CAGR) of 5.60% during the forecast period from 2024 to 2033.
Pneumatic conveying systems are specialized transport solutions that use air pressure to move bulk materials through pipes, tubes, or ducts in industrial settings. These systems are essential in industries such as food processing, pharmaceuticals, chemicals, and manufacturing, where efficient and clean material handling is crucial. The pneumatic conveying systems market has witnessed steady growth due to the increasing demand for automation and material handling efficiency.
Factors driving this growth include advancements in technology, the rising need for safety in handling hazardous materials, and the growing emphasis on minimizing environmental impact. The demand for such systems is primarily fueled by their ability to reduce labor costs, improve process efficiency, and ensure hygienic transport of materials in sensitive industries. Moreover, opportunities exist in emerging economies where industrialization is rapidly expanding, and the rising adoption of Industry 4.0 technologies offers substantial potential for market expansion, particularly in sectors such as food & beverage and pharmaceuticals.
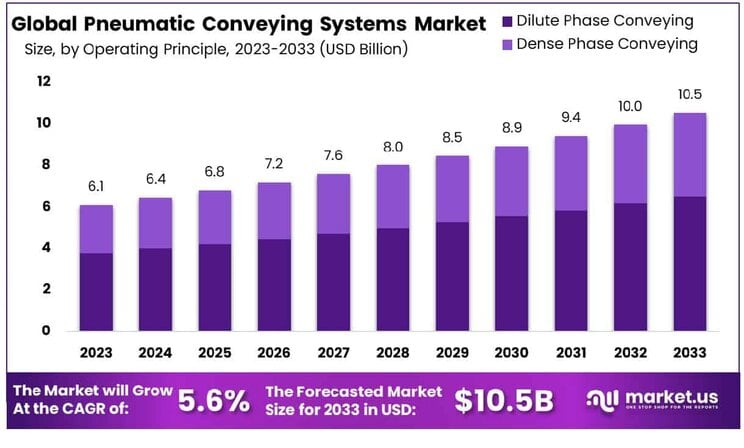
Key Takeaways
- The Pneumatic Conveying Systems Market is projected to reach USD 10.5 Billion by 2033, up from USD 6.1 Billion in 2023, reflecting a CAGR of 5.60% from 2024 to 2033.
- Dilute phase conveying continues to dominate the market, holding a significant 62% share.
- Positive pressure systems lead the market in terms of technology, accounting for 46% of the market share.
- The food industry is the largest end-user of pneumatic conveying systems, commanding a 31% market share.
- Asia-Pacific is the dominant region, holding a significant 34.2% share of the global Pneumatic Conveying Systems Market.
Report Scope
Report Features | Description |
---|---|
Market Value (2023) | USD 6.1 Billion |
Forecast Revenue (2033) | USD 10.5 Billion |
CAGR (2024-2033) | 5.60% |
Segments Covered | By Operating Principle(Dilute Phase Conveying, Dense Phase Conveying), By Technology(Positive Pressure Systems, Vacuum Systems, Combination Systems), By End-Use Industry(Food Industry, Pharmaceuticals, Automotive, Mining , Ceramic, Other End-Use Industries) |
Competitive Landscape | Atlas Copco AB, Cyclonaire Corporation, Coperion GmbH, Dongyang P & F, Flexicon Corporation, Dynamic Air Inc., Gericke AG, VAC-U-MAX, Nol-Tec Systems Inc., Schenck Process Holding GmbH, Other Key Players |
Emerging Trends
- Integration with Industry 4.0: The rise of smart manufacturing and automation is influencing the pneumatic conveying systems market. These systems are increasingly being integrated with sensors, IoT, and machine learning technologies to improve performance monitoring, predictive maintenance, and real-time data analytics. This trend allows for enhanced operational efficiency, reduced downtime, and optimized energy consumption.
- Shift to Energy-Efficient Designs: As industries focus more on sustainability, there is a growing trend toward energy-efficient pneumatic conveying systems. Manufacturers are adopting designs that reduce power consumption while maintaining high throughput. Energy-efficient blowers, lower friction materials, and optimized system configurations are all contributing to reduced operational costs and environmental impact.
- Advancements in Materials and Components: New materials are being used to enhance the durability and performance of pneumatic conveying systems. For example, the introduction of corrosion-resistant alloys, lightweight plastics, and wear-resistant composites in components like pipes, filters, and valves is improving the lifespan and reducing maintenance requirements of these systems.
- Customization for Specific Industry Needs: Pneumatic conveying systems are increasingly being customized to meet the specific needs of various industries. Whether in food processing, pharmaceuticals, or chemicals, systems are being designed with tailored capacity, material handling characteristics, and hygiene standards to meet industry-specific regulations and improve efficiency.
- Automation of System Operations: Another key emerging trend is the increased automation of pneumatic conveying systems. More systems are being designed with automated control features such as variable speed drives, automatic load balancing, and self-cleaning mechanisms, reducing the need for manual intervention, improving reliability, and enhancing productivity.
Top Use Cases
- Food & Beverage Industry: Pneumatic conveying is widely used in food processing plants to transport powders, granules, and other bulk materials like flour, sugar, and spices. These systems are ideal for maintaining hygiene standards and preventing contamination during the transport of raw materials, ensuring product safety and consistency. Pneumatic systems in this sector handle large volumes—up to several tons per hour—ensuring high productivity and reducing manual labor.
- Pharmaceutical Applications: In the pharmaceutical sector, pneumatic conveying systems are employed for transporting active pharmaceutical ingredients (APIs), excipients, and powders. These systems ensure that delicate materials are conveyed safely without degradation. Precision is critical, and pneumatic systems are designed to handle fine powders with a high degree of accuracy, often in cleanroom conditions, to meet strict regulatory standards.
- Chemical Processing: Pneumatic conveying systems are heavily utilized in the chemical industry to move hazardous, corrosive, or fine powders and granules. With the ability to transport materials over long distances and through complex pathways, these systems are well-suited for environments where safety and material integrity are paramount. Capacities can vary widely, with some systems handling up to 100 tons per hour depending on the material type.
- Plastic Processing: In the plastics industry, pneumatic conveying systems are used to move pellets, powders, and other small plastic particles. These systems are crucial for minimizing material loss during production and for handling high-temperature materials that need careful transportation to avoid contamination or degradation.
- Bulk Material Handling in Mining: Pneumatic conveying is often used in the mining industry to transport bulk materials such as coal, sand, and minerals. These systems can handle abrasive materials over long distances, which is particularly useful in remote mining operations where the material needs to be conveyed over challenging terrain. High-capacity systems can move several hundred tons per hour, ensuring efficiency in operations.
Major Challenges
- High Energy Consumption: Despite technological advancements, pneumatic conveying systems remain energy-intensive. The need for continuous airflow and pressure to move bulk materials can result in high electricity usage. For example, energy consumption can reach up to 30-50% of the total operational costs in large-scale systems, making energy efficiency a priority for manufacturers.
- Material Segregation and Degradation: Pneumatic conveying systems can cause segregation of materials due to variations in airflow rates and particle sizes. This is particularly a problem when transporting heterogeneous materials like food powders, where uniform mixing is critical. Additionally, delicate materials may degrade during transport due to excessive turbulence or high velocities within the pipes.
- Dust Emissions and Contamination: Dust formation is a significant issue, particularly when conveying dry, powdered materials. These particles can cause environmental hazards, pose health risks, and contaminate the surrounding environment. Proper filtration systems are required to minimize emissions, but this increases maintenance costs and complexity.
- System Wear and Maintenance: The mechanical components of pneumatic conveying systems are subject to wear and tear, particularly when handling abrasive materials. For instance, pipes, valves, and blowers can degrade over time, increasing the frequency and cost of maintenance. Some systems may require routine inspections and part replacements after just a few years of operation, impacting operational efficiency.
- Limited Flexibility in Material Types: Pneumatic conveying systems may not be suitable for all types of materials. For example, materials that are too sticky, too fragile, or too large in size may not be effectively conveyed through a pneumatic system. These limitations make it difficult to implement pneumatic conveying in some industries without significant modifications or the introduction of additional systems to handle these specific materials.
Top Opportunities
- Expansion in Emerging Markets: With industrialization rapidly growing in emerging markets such as Asia-Pacific, Latin America, and Africa, the demand for pneumatic conveying systems is expected to rise. These regions are increasingly adopting automated and efficient material handling systems across industries such as food processing, chemicals, and pharmaceuticals, opening up substantial growth opportunities.
- Advancements in System Automation: As automation continues to play a larger role in manufacturing, the demand for automated pneumatic conveying systems will rise. Manufacturers are adopting automated systems to reduce labor costs, enhance precision, and improve efficiency. The integration of smart sensors, AI, and machine learning in conveying systems will improve predictive maintenance, reducing downtime and overall operating costs.
- Increasing Demand for Sustainable Solutions: The global push for sustainability is driving the demand for environmentally friendly material handling solutions. Pneumatic conveying systems, being highly customizable, can be optimized to use less energy and generate less waste. Systems that can reduce power consumption by 10-15% or more are particularly attractive to industries aiming to reduce their carbon footprint.
- Customization for Diverse Industries: The need for tailored solutions is growing as industries seek pneumatic conveying systems that can meet specific operational needs, such as handling delicate, hazardous, or high-temperature materials. Custom solutions can drive market growth by offering more specialized applications, ensuring systems are adaptable and efficient across sectors like chemicals, pharmaceuticals, and food production.
- Technological Innovations for Improved Efficiency: Technological innovations in blowers, filtration, and materials handling are likely to drive the future of pneumatic conveying systems. For example, new types of centrifugal blowers offer higher efficiency and reduced maintenance costs. Similarly, the development of advanced filtration technologies promises to reduce dust and enhance system longevity, making these systems more attractive to industries looking to reduce costs and improve performance.
Key Player Analysis
- Atlas Copco AB: Atlas Copco is a leading provider of pneumatic conveying systems, specializing in air treatment, compressors, and vacuum systems. The company focuses on energy-efficient solutions for industries like pharmaceuticals, food processing, and chemicals. It offers comprehensive pneumatic conveying solutions, including both positive pressure and vacuum-based systems.
- Cyclonaire Corporation: Cyclonaire Corporation is known for its innovative pneumatic conveying technologies, offering customized systems for bulk materials like cement, chemicals, and food products. They have a strong market presence in North America and provide solutions that prioritize system efficiency and reliability. Their products are widely used in industries that demand precise material handling.
- Coperion GmbH: Coperion GmbH, a subsidiary of the Hillenbrand Inc., is a global leader in the design and supply of pneumatic conveying systems. The company provides systems for bulk material handling across multiple industries, including plastics, chemicals, and food. It is known for its high-quality engineered solutions and diverse range of conveying equipment.
- Dongyang P & F: Dongyang P & F is a prominent player in the pneumatic conveying market in Asia, providing systems that support industries such as cement, mining, and plastics. The company focuses on energy-efficient conveying technologies and tailor-made solutions.
- Flexicon Corporation: Flexicon Corporation is a well-known manufacturer of bulk material handling systems, including pneumatic conveyors, dust collection, and bulk storage systems. With over 40 years of experience, Flexicon has built a strong reputation in the global market. It serves industries such as food, pharmaceuticals, and chemicals.
Regional Analysis
The Asia-Pacific region is the dominant player in the global pneumatic conveying systems market, holding a significant share of 34.2% in 2023. This dominance is driven by rapid industrialization, particularly in China, India, Japan, and South Korea, where key sectors like chemicals, pharmaceuticals, food and beverage, and mining are expanding. The increasing demand for efficient material handling systems, combined with the region’s growing focus on automation and sustainability, further fuels market growth. With Southeast Asia’s emerging industrial base and rising investments in smart manufacturing, Asia-Pacific is set to continue leading the market, offering substantial growth opportunities in the years ahead.
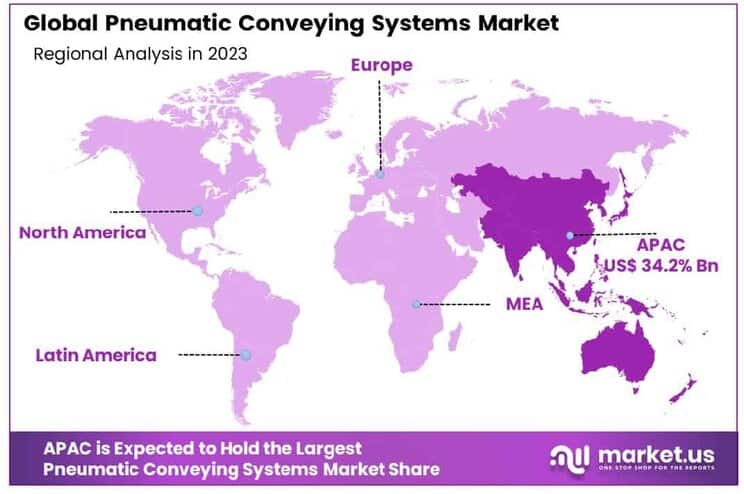
Recent Developments
- In 2023, Addtech Process Technology, a division within the Addtech Group, finalized an agreement to acquire 100% of Clyde Holding Limited. Clyde, based in Doncaster, UK, specializes in pneumatic conveying systems, primarily serving the process and energy sectors. With global operations, the company has over 49 employees and generates annual sales of about GBP 12 million.
- In March 2023, Coperion, alongside Coperion K-Tron and Gabler Engineering, presented advanced process solutions at Interpack 2023 in Düsseldorf. This year marked the first joint appearance with Gabler Engineering, which was integrated into Coperion’s portfolio in 2022. With over 115 years of expertise, Gabler showcases tailored systems for the confectionery and pharmaceutical industries, such as extruders and molding lines. They featured the KM-40 extruder at their booth, a key piece of machinery for producing chewy candies and gum.
- In 2023, Volkmann USA introduced its Waste Reduction Vacuum Conveying System. The Volkmann VS system efficiently captures and recycles excess ingredients during processing, allowing for immediate reuse or storage for later application, supporting waste reduction in manufacturing processes.
Conclusion
The pneumatic conveying systems market is poised for steady growth driven by increasing industrial automation, the demand for energy-efficient solutions, and the need for safe and efficient material handling across various industries. With ongoing advancements in technology, particularly in system automation, energy efficiency, and integration with Industry 4.0, these systems are becoming increasingly versatile and tailored to the specific needs of sectors like food processing, pharmaceuticals, and chemicals. As industrialization continues to rise in emerging markets and sustainability becomes a priority globally, the market offers substantial opportunities for innovation and expansion. However, challenges such as high energy consumption, material degradation, and the need for specialized solutions will need to be addressed to maintain long-term market growth and competitiveness.
Discuss Your Needs With Our Analyst
Please share your requirements with more details so our analyst can check if they can solve your problem(s)
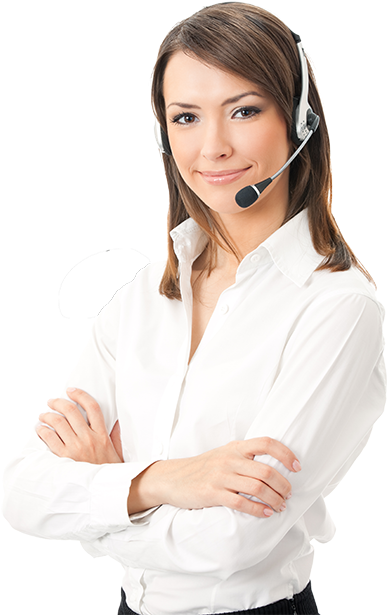