Table of Contents
Introduction
The global Intumescent Coatings Market is witnessing steady growth, with its size projected to reach USD 1.81 Billion by 2033, up from USD 1.13 Billion in 2023, reflecting a compound annual growth rate (CAGR) of 4.8% during the forecast period from 2023 to 2033.
This market growth is primarily driven by the increasing demand for fire protection in both residential and commercial buildings, where intumescent coatings are widely used due to their ability to enhance fire resistance. The rise in construction activities and stringent fire safety regulations across various regions further boost the demand for these coatings.
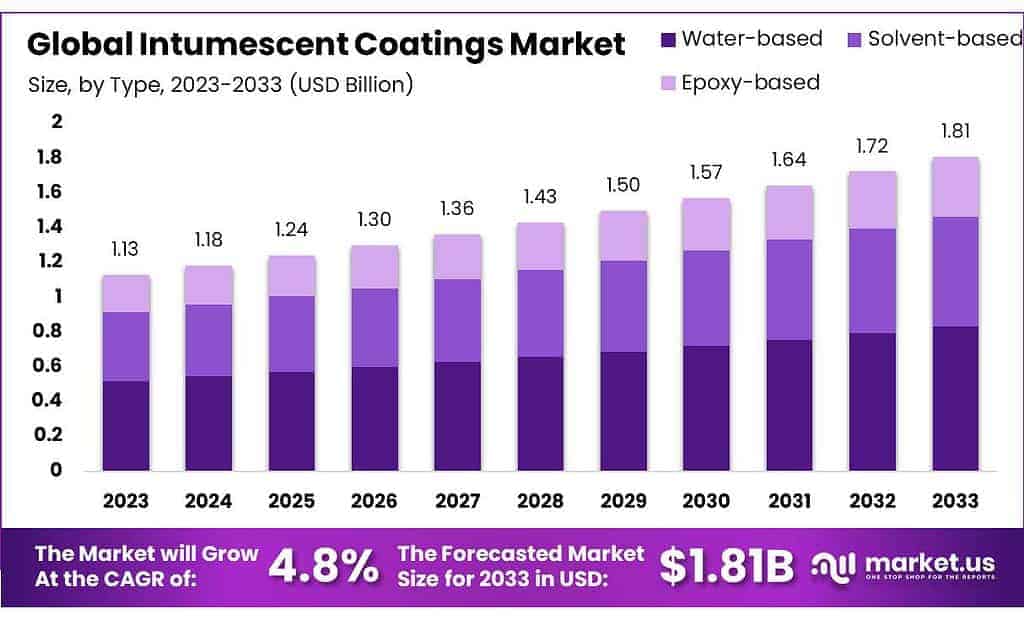
Additionally, advancements in technology and product formulations have led to more efficient, durable, and environmentally friendly coatings, contributing to the market’s popularity. The growing emphasis on sustainability, coupled with increased awareness about fire safety, has created ample opportunities for market expansion, particularly in emerging economies where infrastructure development is accelerating. Market players are capitalizing on these opportunities by innovating new products and expanding their geographical reach, especially in regions such as Asia Pacific, where industrial growth and urbanization are rapidly increasing.
Furthermore, the expansion of industries such as oil and gas, automotive, and marine, where fire-resistant materials are critical, is expected to further drive market growth. As the demand for high-performance and long-lasting fire protection coatings rises, the global Intumescent Coatings Market is poised for significant expansion in the coming years.
Intumescent Coatings Statistics
- Intumescent coatings have been integral in protecting steel structures from fire for about 40 years.
- When exposed to fire, these coatings swell to create a protective barrier that can last up to four hours, significantly delaying the steel from reaching its critical failure temperature of approximately 400°C.
- Thin-film intumescents are often single-component solvent or water-based products that have dry film thicknesses (DFTs) of less than 5 millimeters.
- Thick-film coatings are typically solvent-free and epoxy-based which have DFTs up to 25 millimetres.
- Standards like BS 476 and EN 13381 for cellulosic fires, and UL 1709 and ISO 22899–1 for hydrocarbon fires, provide benchmarks for performance.
- Standard tests like NORSOK M 501 and UL 2431 ensure these coatings meet durability requirements.
- The intumescent coating behavior is characterized by expansion and mass loss, producing a foam char with a volume that varies from 5 to 200 times its original volume.
- The steel plates are 100mm squared and 4mm thick, coated on one side with different dry film thicknesses, and tested in a cone calorimeter as prescribed by the standard E1354-04.
- For intumescent materials values between 0.7 and 0.95 can be found in the literature, where the lower value is normally used for the virgin material state, and values of 0.8, 0.9, and 0.95 are used for the intumescence char surface, see.
- The intumescent coating-specific heat was considered constant and equal to 1000 J/kgK.
- Fulfillment of the research objectives resulted in the development of a coating with R120 fire resistance.
- The coating thickness is to be 0.4–0.5 mm. To achieve higher fire resistance (R60 or more) the coating should include a vinyl acetate derivative as a binder.
- The target components ratio in this case is to be close to 3.5/1/1.5, while the coating thickness should be kept at 1.6–1.8 mm.
- A step-by-step study of the intumescent char formation in the temperature range of 200–800°С was carried out by exposing the same sample of intumescent coating to a gradually rising set of temperatures.
- The thickness of dry coatings was measured using a Qnix1500 magnetic thickness gauge.
- At the same time, the fire resistance of 1.95 mm thick IC6 coating was found to be 42 min, compared to 56 min for ІС1.
- With DFTs of up to 5000μm, thin film intumescent protective coatings can be solvent or water-based and come as a single pack designed to withstand cellulosic fires, which occur when the fuel source is primarily made up of wood or paper.
- Thick film intumescent protective coatings are usually solvent-free and epoxy-based, with DFTs up to 25,000μm.
Emerging Trends
- Increasing Focus on Sustainability: There is a growing trend towards eco-friendly intumescent coatings. Manufacturers are focusing on developing low-VOC (volatile organic compounds) and non-toxic coatings that provide fire protection while minimizing environmental impact. This aligns with the increasing demand for green building materials.
- Technological Advancements in Formulations: Advances in nanotechnology and advanced polymers are driving the development of high-performance intumescent coatings. These innovations improve the coatings’ fire resistance, durability, and ease of application, making them more effective in a variety of industries.
- Growth in Commercial Construction: The commercial construction sector is driving demand for intumescent coatings, particularly in high-rise buildings and office spaces. These coatings provide essential fire protection, meeting stringent safety regulations in urban infrastructure projects.
- Expansion in Emerging Economies: Rapid urbanization and industrial growth in emerging markets, especially in Asia Pacific, are creating new opportunities for intumescent coatings. As these regions implement stricter building codes, demand for fire-resistant materials is expected to increase significantly.
- Focus on Aesthetic Integration: Modern intumescent coatings are being developed to combine fire resistance with aesthetic appeal. These coatings are designed to be thin and less intrusive, maintaining the visual appeal of structures while providing reliable fire protection, making them popular for architectural applications.
- Increased Adoption in Industrial Sectors: Intumescent coatings are increasingly being used in industries like oil and gas, automotive, and marine, where fire safety is critical. The demand for protective coatings in hazardous environments is driving growth in these sectors.
- Regulatory Pressures for Fire Safety: Governments worldwide are tightening fire safety regulations, particularly in residential and commercial buildings. As compliance with fire safety standards becomes more critical, the demand for intumescent coatings that meet these requirements continues to rise.
- Rise in Retrofit and Renovation Projects: With the growing emphasis on fire safety in existing buildings, there is an increasing trend toward retrofitting older structures with intumescent coatings. This is driven by stricter fire safety regulations and the need to upgrade buildings to modern safety standards without significant structural alterations.
- Growing Demand in Infrastructure Projects: Infrastructure projects, including bridges, tunnels, and transportation networks, are increasingly incorporating intumescent coatings. These coatings provide essential fire protection in critical structures, especially in high-risk areas like transportation hubs, where passenger safety is a top priority.
- Integration with Fireproofing Systems: Intumescent coatings are increasingly being integrated with other fireproofing solutions, such as passive fire protection systems. This combination enhances the overall safety and effectiveness of fire protection strategies, making them an attractive option for large-scale industrial and commercial projects.
Use Cases
- Fire Protection in High-Rise Buildings: Intumescent coatings are widely used in high-rise buildings to protect structural steel from fire. When exposed to high heat, the coating expands, creating a thermal barrier that helps maintain the integrity of the building’s structure, providing critical time for evacuation and firefighting.
- Industrial Applications: In industries such as oil and gas, intumescent coatings are applied to pipelines, tanks, and other critical infrastructure. These coatings protect against potential fires in hazardous environments, ensuring safety in high-risk areas like refineries and chemical processing plants.
- Marine and Offshore Platforms: Intumescent coatings are extensively used in the marine sector to safeguard ships, offshore oil rigs, and platforms from fire damage. These coatings provide an added layer of protection in harsh marine environments, where fire risks are high, and safety standards are stringent.
- Fire Protection in Transport Infrastructure: Intumescent coatings are applied to critical transport infrastructure, including tunnels, bridges, and railway stations. These coatings help prevent the spread of fire, ensuring the safety of passengers and minimizing damage to these vital structures during a fire incident.
- Fireproofing for Electrical Equipment: Intumescent coatings are used to protect electrical cables, panels, and other equipment from fire risks. In critical systems like power plants and data centers, these coatings help prevent electrical fires, ensuring the continued operation of essential services.
- Retrofit in Existing Buildings: In renovation and retrofit projects, intumescent coatings are applied to existing buildings to enhance fire resistance without compromising the aesthetics. This is particularly useful for upgrading the fire safety of older structures to meet modern regulations and standards.
- Fire Protection for Steel Structures: Intumescent coatings are commonly used to protect steel beams and columns in construction projects. These coatings prevent the steel from losing its strength under high heat, ensuring the structural integrity of buildings and other construction projects during a fire.
- Fire Resistance in Storage Warehouses: In warehouses storing hazardous materials, intumescent coatings are applied to walls, ceilings, and beams. These coatings reduce the risk of fire spreading and provide essential protection in facilities where fire risks are heightened due to the nature of stored goods.
- Application in Aerospace Industry: Intumescent coatings are used in aerospace applications to protect aircraft and spacecraft components from fire damage. These coatings are applied to fuel tanks, engines, and other critical parts, ensuring safety during flight and preventing catastrophic fires in case of accidents or system malfunctions.
- Fire Protection in Commercial Kitchens: In commercial kitchens and restaurants, intumescent coatings are applied to hoods, ducts, and ventilation systems. These coatings help prevent grease fires from spreading, ensuring the safety of kitchen staff and customers while complying with fire safety regulations in food service establishments.
- Construction of Fire-Resistant Doors and Windows: Intumescent coatings are used in the manufacturing of fire-resistant doors and windows. When exposed to fire, these coatings expand to form a protective barrier, delaying the spread of fire and allowing occupants more time to evacuate safely during a fire emergency.
Major Challenges
- Cost of Application: The application of intumescent coatings can be expensive, especially when used in large-scale projects. High material costs, along with the need for specialized application techniques and skilled labor, can increase overall project expenses, making them less accessible for budget-conscious projects.
- Environmental Concerns: Despite advances in eco-friendly formulations, some intumescent coatings still contain chemicals that can be harmful to the environment. Regulatory pressure for greener alternatives is rising, and the development of low-VOC, non-toxic coatings remains a challenge for manufacturers looking to meet sustainability goals.
- Limited Durability: While intumescent coatings are effective in fire protection, their durability can be compromised under certain conditions, such as exposure to extreme weather, abrasion, or UV light. This requires regular maintenance or reapplication, which can add to long-term costs and inconvenience for end-users.
- Compatibility with Different Substrates: Intumescent coatings may not always bond effectively with all types of substrates, such as metals, concrete, or wood. This can lead to uneven performance and reduced effectiveness in fire protection, requiring additional surface treatments or primers to ensure proper adhesion.
- Complex Application Process: The application of intumescent coatings requires precision and expertise. If not applied correctly, the coating may fail to provide the desired level of fire protection. Proper surface preparation, environmental conditions, and correct application techniques are essential, which can make the process labor-intensive.
- Regulatory Compliance and Certification: Different regions have varying fire safety regulations, making it challenging for manufacturers to ensure their products meet all required standards globally. Intumescent coatings must undergo rigorous testing and certification to comply with local fire safety codes, adding complexity and cost to product development.
- Aesthetic Limitations: Traditional intumescent coatings can sometimes be thick and visually unappealing, especially when applied to exposed surfaces. Though advancements have been made, achieving a balance between high fire protection and maintaining the aesthetic integrity of structures remains a challenge in certain applications.
- Performance in High-Temperature Environments: Intumescent coatings are generally effective up to certain temperatures. However, in extremely high-temperature environments, such as in industrial or fire-fighting applications, the coatings may not perform as expected. This limits their use in some specialized applications where higher heat resistance is required.
- Long Drying Time: Intumescent coatings often require extended curing times, which can delay construction or renovation projects. This is particularly challenging in fast-paced industries or projects with tight deadlines, where longer drying periods can increase the overall time and costs of the project.
- Surface Preparation Requirements: For intumescent coatings to perform optimally, the substrate surface must be properly prepared. This includes cleaning, priming, and sometimes sanding the surface. Inadequate preparation can lead to poor adhesion and reduced fire resistance, making the application process more complex and time-consuming.
- Temperature Sensitivity During Application: Intumescent coatings require specific temperature conditions for optimal application and curing. If applied in extreme heat or cold, the coating may not cure properly, leading to compromised fire protection. This sensitivity can be a significant challenge in regions with variable climates or outdoor applications.
- Limited Knowledge and Expertise: The specialized nature of intumescent coatings means that a skilled workforce is required for both application and maintenance. The lack of trained professionals in certain regions or industries can result in improper application, reducing the effectiveness of the coatings and posing safety risks.
Market Growth Opportunities
- Growth in the Construction Sector: The expanding construction industry, especially in emerging economies, presents significant opportunities for intumescent coatings. As new buildings and infrastructure projects are developed, the demand for fire-resistant coatings is increasing to meet stricter fire safety regulations, creating a robust growth opportunity for manufacturers.
- Rising Awareness of Fire Safety: With increasing awareness of fire hazards and safety, particularly in commercial and industrial sectors, there is a growing preference for passive fire protection solutions like intumescent coatings. This trend is driving demand for these products, especially in regions with stringent fire safety standards.
- Expansion in Retrofitting Market: As older buildings are upgraded to meet modern safety standards, the market for retrofitting intumescent coatings is expanding. This provides a substantial growth opportunity for manufacturers, especially in developed countries where building codes are becoming more stringent and fire protection retrofits are required.
- Applications in Renewable Energy: The renewable energy sector, especially wind and solar farms, presents a unique opportunity for intumescent coatings. These coatings are used to protect critical infrastructure like turbines and electrical equipment from fire risks, thus expanding the market potential within the growing renewable energy industry.
- Technological Advancements: Continuous improvements in the performance of intumescent coatings, such as enhanced durability, quicker drying times, and more aesthetically pleasing finishes, are driving their adoption. Technological advancements in these areas create significant growth opportunities by meeting the evolving needs of various industries.
- Increasing Demand in the Oil & Gas Industry: The oil and gas sector, where fire hazards are particularly high, represents a growing market for intumescent coatings. These coatings help protect pipelines, storage tanks, and refineries, creating growth prospects as the industry continues to expand globally.
- Government Regulations and Standards: The implementation of stricter government regulations regarding fire safety is a major driver of demand for intumescent coatings. As fire safety standards become more rigorous, businesses will increasingly turn to these coatings to comply with new laws and ensure the protection of their assets and people.
- Rising Focus on Green Building Initiatives: The growing trend toward sustainable and green buildings presents a promising opportunity for intumescent coatings. These coatings can contribute to meeting environmental standards while providing necessary fire protection, making them an attractive option for green building projects worldwide.
- Market Expansion in Emerging Economies: As developing countries invest in infrastructure and urbanization, the demand for fire protection products, including intumescent coatings, is rising. This market expansion in regions like Asia-Pacific, Latin America, and the Middle East presents a significant growth opportunity for manufacturers to tap into new markets.
- Integration with Other Fire Safety Systems: The integration of intumescent coatings with other fire safety systems, such as fire alarms and sprinklers, enhances their effectiveness and creates new market opportunities. This integrated approach is particularly appealing in commercial and industrial applications where comprehensive fire safety solutions are essential.
Key Players Analysis
- Akzo Nobel N.V. is a leading player in the intumescent coatings market, offering high-performance fire protection solutions across various industries, including construction, marine, and oil & gas. The company focuses on delivering advanced coatings that ensure safety while meeting international fire safety standards.
- Jotun provides a range of intumescent coatings, primarily serving the marine, offshore, and industrial sectors. Their products offer superior fire protection for steel structures, with a focus on sustainability and environmental impact, making Jotun a preferred choice in demanding fireproofing applications.
- Contego International Inc. specializes in fire protection coatings, including intumescent solutions that are widely used in commercial and industrial construction. The company is known for its innovative fire safety products that offer long-lasting protection, meeting rigorous fire regulations across various regions.
- Hempel A/S offers a wide array of coatings, including intumescent fire protection coatings, for industries like marine, oil & gas, and construction. Their products provide exceptional fire resistance and durability, with an emphasis on reducing environmental impact and improving the sustainability of their coatings.
- No-Burn Inc. focuses on intumescent coatings for residential, commercial, and industrial applications. Their fire-resistant coatings are known for their non-toxic nature and ease of application, catering to a wide range of sectors where fire safety is a top priority.
- Nullifire provides advanced intumescent fire protection coatings primarily for steel structures, offering long-lasting performance under extreme conditions. Their products are widely used in the construction and industrial sectors, ensuring fire safety without compromising the aesthetic appearance of buildings.
- The Sherwin-Williams Company offers a comprehensive portfolio of intumescent coatings for industrial, commercial, and residential buildings. Their products deliver reliable fire protection while also providing additional benefits such as corrosion resistance and easy application, making them a leader in the global market.
- Carboline is a key player in the intumescent coatings sector, providing high-performance solutions that protect steel structures from fire. Their coatings are widely used in industrial, commercial, and marine applications, offering a combination of fire resistance and durability to ensure safety in demanding environments.
- Albi Protective Coatings offers innovative intumescent coatings that provide fire protection for steel and other substrates. Their products are used across various industries, including construction, manufacturing, and energy, offering high levels of fire resistance while maintaining structural integrity in case of fire.
- Isolatek International is a leading supplier of passive fire protection products, including intumescent coatings. Their solutions are used to protect structural steel in the construction and industrial sectors, ensuring compliance with fire safety codes while offering a range of products suited to various applications.
- Rudolf Hensel GmbH is a German company specializing in intumescent fire protection coatings. Their products are designed for use in industrial, commercial, and construction applications, providing high-quality fire protection that is both durable and aesthetically pleasing, while meeting stringent safety regulations.
- PPG Industries is a global leader in coatings, offering a wide range of intumescent fire protection coatings. The company’s products are widely used in industries such as construction, automotive, and oil & gas, providing reliable fire resistance and contributing to the safety and longevity of critical infrastructure.
- 3M provides a diverse range of fire protection solutions, including intumescent coatings for both industrial and commercial applications. Their products are known for their high performance, ease of use, and ability to meet international fire safety standards, positioning 3M as a trusted brand in fireproofing.
- Sika AG offers a variety of intumescent fire protection coatings designed for both steel and concrete structures. Their coatings are used across construction, infrastructure, and industrial sectors, providing long-lasting fire resistance while also ensuring environmental compliance and sustainability in building projects.
- BASF SE offers advanced intumescent coatings that provide superior fire protection for a wide range of applications. Their products are particularly known for their environmental benefits and are used in industries like construction, oil & gas, and automotive, ensuring enhanced safety and structural integrity during fire incidents.
Conclusion
In conclusion, the Intumescent Coatings Market is poised for steady growth, driven by increasing demand for fire protection across various industries, including construction, oil and gas, and renewable energy. The market’s expansion is supported by rising awareness of fire safety, stricter regulations, and ongoing technological advancements that enhance the performance and aesthetics of these coatings. While challenges such as high costs, environmental concerns, and the need for specialized applications remain, the ongoing development of eco-friendly formulations and the growth of emerging markets present significant opportunities for growth.
As the construction industry continues to thrive and retrofitting projects become more common, intumescent coatings will play a vital role in ensuring safety and compliance. Manufacturers who can innovate and address industry needs, particularly with sustainable solutions, are well-positioned to capture a larger share of this expanding market.
Discuss Your Needs With Our Analyst
Please share your requirements with more details so our analyst can check if they can solve your problem(s)
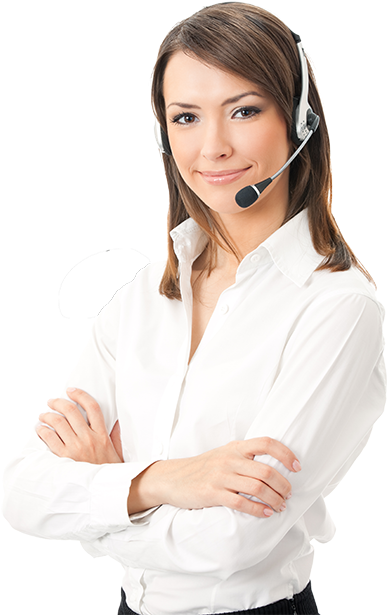