Table of Contents
Introduction
The Global Industrial Computed Tomography Market is projected to expand from USD 520.8 million in 2023 to approximately USD 1,221.7 million by 2033, achieving a compound annual growth rate (CAGR) of 8.9% from 2024 to 2033.
Industrial Computed Tomography (CT) is a sophisticated imaging technique that employs computer-processed combinations of numerous X-ray measurements taken from different angles to produce cross-sectional (tomographic) images of specific areas of a scanned object, allowing the user to see inside the object without cutting it. The Industrial Computed Tomography Market is expanding due to its increased adoption in sectors like automotive, aerospace, electronics, and material science for quality control, failure analysis, and 3D metrology.
Growth factors include technological advancements that improve image quality and speed while reducing costs, and stringent safety regulations which demand high precision in manufacturing processes. Additionally, the shift towards automation and high-volume production creates substantial demand for non-destructive testing techniques. Opportunities in the market are vast, particularly in emerging markets where industries are just beginning to adopt advanced quality assurance methods, and in the development of portable CT scanners that could bring this powerful diagnostic tool directly to the production line.
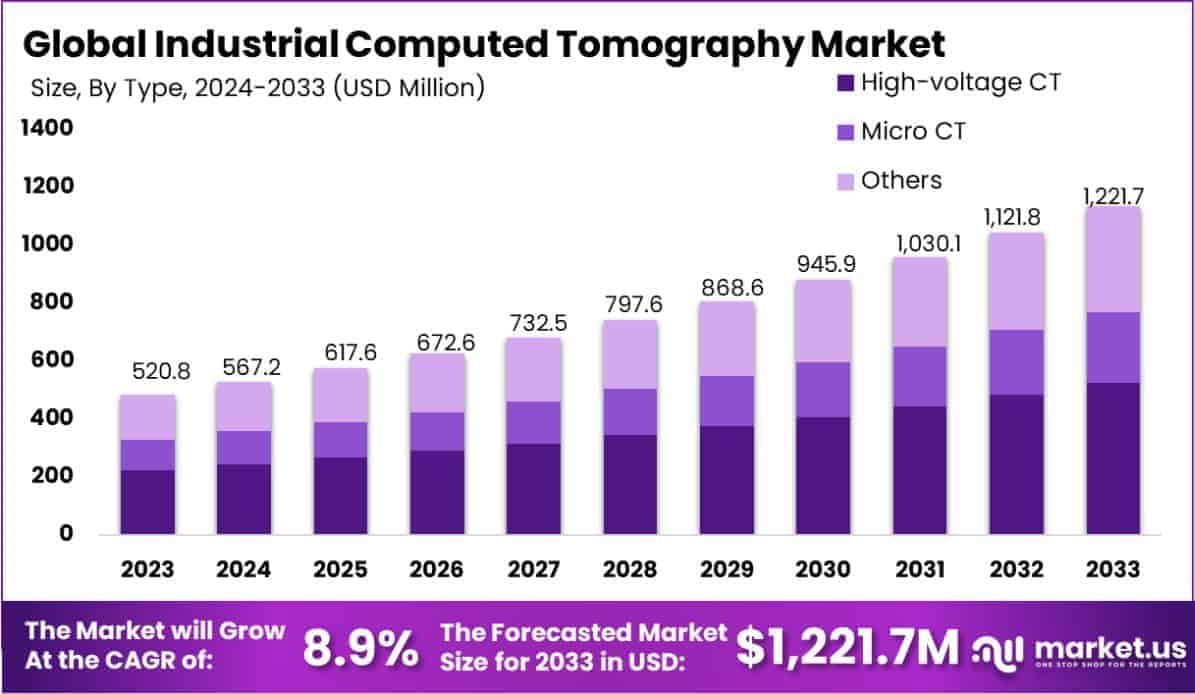
Key Takeaways
- The Industrial CT Market is expected to grow significantly, with its value projected to increase from USD 520.8 million in 2023 to approximately USD 1,221.7 million by 2033, at a Compound Annual Growth Rate (CAGR) of 8.9%.
- In the offerings category, Equipment held the largest share at 52.1%, indicating a strong demand for industrial CT hardware.
- High-voltage CT was the most dominant type, accounting for 43.1% of the market, reflecting its critical role in high-energy industrial applications.
- Fan-beam CT was the leading scanning technique with 44.6% market share, favored for its efficiency and accuracy.
- Flaw Detection and Inspection was the top application, holding a 25.4% share, underscoring its importance in quality control and assurance processes.
- The Automotive sector dominated the vertical applications of Industrial CT, with a 27.2% share, highlighting its essential use in automotive manufacturing and testing.
- Asia Pacific was the leading region with a 34.1% market share, amounting to USD 177.5 million in revenue, which signals robust industrial activity and technological adoption in this region.
Report Scope
Report Features | Description |
---|---|
Market Value (2023) | USD 520.8 Billion |
Forecast Revenue (2033) | USD 986.8 Billion |
CAGR (2024-2033) | 8.9% |
Segments Covered | By Offering(Equipment, Services), By Type(High-voltage CT, Micro CT, Others), By Scanning Technique(Fan-beam CT, Cone-beam CT, Others), By Application(Flaw Detection and Inspection, Failure Analysis, Assembly Analysis, Dimensioning and Tolerancing Analysis, Others), By Vertical(Oil & Gas, Aerospace and Defense, Automotive, Electronics, Others) |
Competitive Landscape | GE Measurement & Control Solutions, Siemens AG, Nikon Metrology, ZEISS Group, YXLON International, North Star Imaging, Rigaku Corporation, Carl Zeiss Industrial Metrology, Shimadzu Corporation, Werth Messtechnik, 3D Systems, Avonix Imaging, Other Key Players |
Emerging Trends
- Integration with Artificial Intelligence (AI): Industrial CT is increasingly combining with AI to improve defect detection and material analysis. AI algorithms can analyze large volumes of CT scan data more efficiently, identifying hidden issues that traditional methods might miss. AI enhances predictive maintenance, offering manufacturers proactive insights. This trend is especially growing in the automotive and aerospace industries, where precision is critical.
- Portable and Compact CT Systems: New advancements in CT scanner technology have led to the development of smaller, more portable systems. These compact units allow for on-site inspections, reducing downtime and improving efficiency in industries such as manufacturing and construction. Portable CT is gaining traction due to its ability to scan large parts directly at the production floor.
- Higher Resolution Imaging: With continuous advancements in detector technology, the resolution of industrial CT scanners is improving. The ability to capture more detailed images is driving the adoption of CT in high-precision industries like electronics and semiconductor manufacturing. Higher resolution allows for the detection of minute defects, cracks, and voids within materials, helping to ensure quality control.
- Increased Use in Additive Manufacturing: Industrial CT is becoming an essential tool for quality control in additive manufacturing (3D printing). As the use of 3D printing in industries like aerospace and healthcare grows, CT is crucial in ensuring the integrity and safety of 3D-printed components. It is used to check for internal defects, voids, and material inconsistencies without destroying the part.
- Integration with Digital Twin Technology: CT imaging is being used alongside digital twin technologies for virtual simulations of physical objects. This combination allows manufacturers to simulate real-world conditions for their products, identify weaknesses, and improve product designs before production. It also enables ongoing monitoring of assets throughout their lifecycle.
Top Use Cases
- Non-destructive Testing (NDT) in Aerospace: Industrial CT is widely used in the aerospace sector to inspect complex parts such as turbine blades, engine components, and structural elements. CT allows for internal defect detection like cracks, voids, and inclusions that could compromise safety. The aerospace industry benefits from this method’s ability to check parts without the need for disassembly, saving time and reducing costs.
- Automotive Manufacturing and Quality Control: In automotive production, CT is applied for ensuring the quality of cast and forged parts, such as engine blocks and transmission components. It helps in detecting manufacturing defects like porosity, voids, and wall thickness inconsistencies, ensuring that the parts meet stringent quality standards. This use case is essential for improving product safety and performance.
- Electronics Inspection: CT is used in the electronics industry to inspect circuit boards and microelectronic components. It identifies issues like solder joint failures, wire bonding defects, and internal short circuits, which are difficult to detect through traditional visual inspection methods. With the growing complexity of electronic components, CT ensures that defective parts are identified and rectified before reaching consumers.
- Additive Manufacturing & 3D Printing: CT plays a crucial role in inspecting 3D-printed parts for internal defects such as voids, porosity, or structural weaknesses. This is critical for industries such as aerospace, healthcare, and automotive, where safety and precision are paramount. CT ensures the integrity of the printed part without damaging it, which is essential for high-value, complex components.
- Material Analysis and Failure Investigation: Industrial CT is extensively used to investigate material failures, providing insights into the root causes of fractures or breakdowns. For example, in the energy sector, CT scans are used to analyze turbine blades or reactor components that have experienced fatigue, helping to extend the life cycle of expensive machinery and prevent costly breakdowns.
Major Challenges
- High Initial Investment: The cost of industrial CT equipment can be prohibitive, particularly for small and medium-sized enterprises (SMEs). The price of high-resolution CT scanners, combined with installation and maintenance costs, may prevent some companies from adopting this technology. This financial barrier limits the widespread use of CT, particularly in industries with tighter budgets.
- Data Processing Time: While industrial CT offers high-resolution images, the data generated from scans can be vast and complex. Processing and analyzing this data can take significant time and computational power, particularly for larger parts or intricate designs. As parts increase in complexity, the time needed to produce actionable results can also increase, which can delay decision-making.
- Limited Material Penetration: Although industrial CT is effective for many materials, it has limitations when it comes to materials that are highly dense or thick. For example, metals like tungsten or lead can be difficult to scan thoroughly due to their high density, which limits the technology’s effectiveness in certain industries, such as heavy manufacturing and military applications.
- Resolution vs. Scan Speed: There is often a trade-off between resolution and scanning speed. High-resolution scans take longer to complete, which can slow down production timelines. This is particularly problematic in industries where rapid testing and quick turnaround times are critical, such as in automotive and electronics manufacturing.
- Training and Expertise Requirements: Industrial CT systems are highly specialized, requiring trained operators and engineers to properly manage and interpret the scan data. There is a shortage of skilled professionals with expertise in both operating CT systems and analyzing complex scan results. This skill gap can lead to operational inefficiencies or misinterpretation of scan data.
Top Opportunities
- Expansion in Emerging Markets: As industrialization accelerates in developing economies, the demand for advanced testing and quality control methods like industrial CT is expected to rise. Countries in Asia-Pacific, such as China and India, are witnessing rapid industrial growth, which is likely to drive the adoption of CT for non-destructive testing, particularly in automotive, aerospace, and manufacturing sectors.
- Rising Demand in 3D Printing: The growing use of 3D printing in industries like aerospace, automotive, and healthcare is creating a strong demand for industrial CT. CT is essential for inspecting the internal structure of 3D-printed parts, ensuring they are free from defects. As additive manufacturing continues to evolve, the need for high-quality inspection will likely fuel further growth in the industrial CT market.
- Advancements in CT Technology: Continuous improvements in CT scanner technology, such as faster scan times, higher resolution, and better data processing capabilities, create opportunities for increased adoption. These advancements make CT an even more attractive solution for industries that require fast, reliable, and non-invasive inspections.
- Increased Focus on Quality Control and Safety Standards: As industries face growing pressure to meet stricter quality standards and safety regulations, industrial CT is becoming more widely adopted for quality assurance purposes. From the automotive sector ensuring crash safety to the aerospace industry ensuring part integrity, CT offers a reliable way to meet these increasing regulatory demands.
- Integration with Industry 4.0 and IoT: The integration of industrial CT with Industry 4.0 technologies, including the Internet of Things (IoT) and automation systems, presents an opportunity for companies to monitor and analyze manufacturing processes in real-time. This integration enables predictive maintenance, reducing downtime and improving the overall efficiency of industrial operations.
Regional Analysis
Asia Pacific Dominating the Industrial Computed Tomography Market with the Largest Market Share (34.1% in 2023)
The Asia Pacific region holds the largest market share in the Industrial Computed Tomography (CT) market, accounting for an impressive 34.1% in 2023, valued at USD 177.5 million. This dominant position is primarily driven by the rapid industrialization, technological advancements, and growing demand for precision in manufacturing and quality control across key countries such as China, Japan, South Korea, and India. The increasing adoption of Industrial CT systems in sectors like automotive, aerospace, electronics, and manufacturing is propelling growth in the region.
Furthermore, the presence of leading manufacturers, coupled with rising investments in infrastructure and R&D, strengthens the regional market. The growing emphasis on automation and smart manufacturing technologies, including non-destructive testing (NDT) and inspection, further accelerates the uptake of Industrial CT solutions. With expanding industrial sectors and a robust technological landscape, Asia Pacific is expected to maintain its leadership in the global Industrial CT market in the coming years.
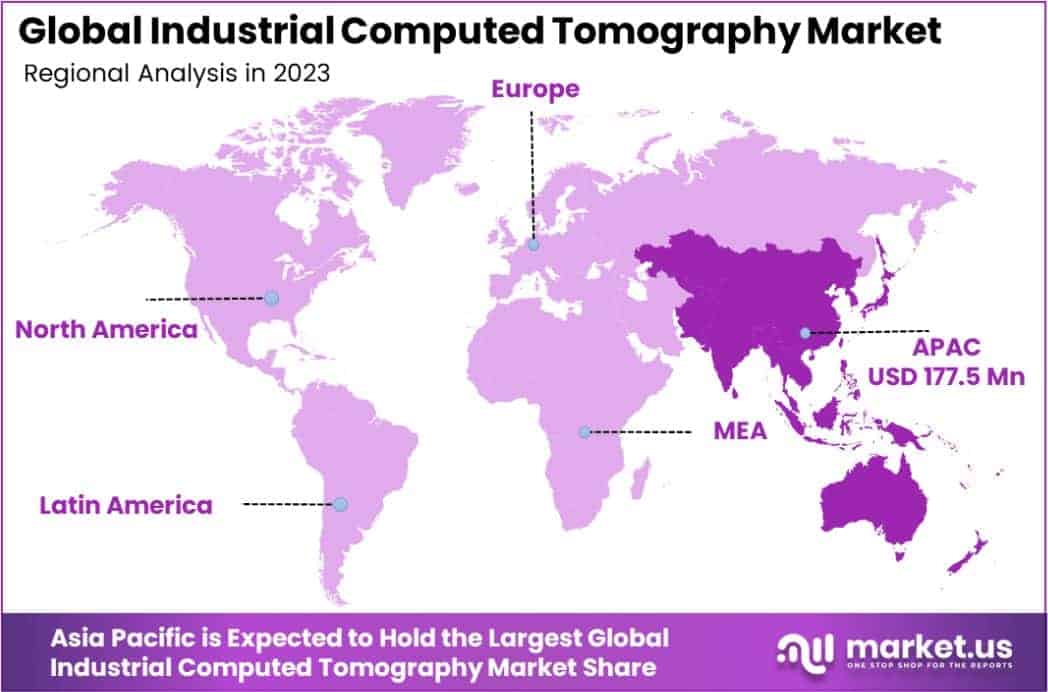
Recent Developments
- In 2023, InVision Technologies secured ownership of YXLON International, a prominent provider of x-ray diffraction and non-destructive testing solutions based in Germany. The transaction, valued at €38.6 million ($41.7 million), reinforced InVision’s position in advanced inspection technologies.
- In 2023, Nikon introduced a large-scale X-ray CT system, VOXLS 40 C 450, designed for precision and versatility. This system supports industries like aerospace, automotive, and research by inspecting components of varying sizes and densities, ensuring accurate and reliable analysis.
- In 2023, Carl Zeiss Meditec AG acquired Dutch Ophthalmic Research Center (D.O.R.C.), broadening its offerings in ophthalmic care. This strategic move strengthened its solutions for treating diverse eye conditions, including cataracts, glaucoma, and retinal disorders.
- On April 30, 2024, Waygate Technologies revealed the Krautkrämer CL Go+, a cutting-edge ultrasonic thickness gauge. The device is tailored for industries like aerospace and automotive, offering precise measurements for metals, plastics, and composites while supporting multiple upgrade options.
- In 2024, GE HealthCare reached an agreement to acquire MIM Software Inc., a company specializing in AI-driven imaging solutions. MIM’s innovations, widely used in diagnostics and oncology, promise to enhance healthcare standards globally.
- In 2023, Canon Medical Systems launched new CT scanners with an advanced platform integrating AI for improved workflows and image quality. These systems are designed to meet increasing diagnostic demands while addressing the challenge of limited radiology staffing.
- In January 2024, NeuroLogica Corp. announced that its OmniTom Elite PCD earned recognition as an Innovative Technology by Vizient, Inc. This designation highlights its cutting-edge features for medical imaging, showcased during a major healthcare technology event.
Conclusion
The Industrial Computed Tomography (CT) market is on a trajectory of significant growth and innovation, driven by the escalating demand for non-destructive testing methods across various industries. With a projected compound annual growth rate of 8.9% through 2033, this market is expanding due to advances in technology that enhance imaging speed and quality while reducing costs. The adoption of industrial CT in critical sectors such as automotive, aerospace, and electronics for tasks like quality control, failure analysis, and 3D metrology underscores its increasing value. Additionally, the integration of artificial intelligence and the development of portable CT systems are set to revolutionize how industries conduct material inspection and quality assurance, particularly in emerging markets. This surge in technological integration and capability enhancement positions the industrial CT market as a cornerstone of modern manufacturing and quality control, promising improved efficiency and reliability in production processes worldwide.
Discuss Your Needs With Our Analyst
Please share your requirements with more details so our analyst can check if they can solve your problem(s)
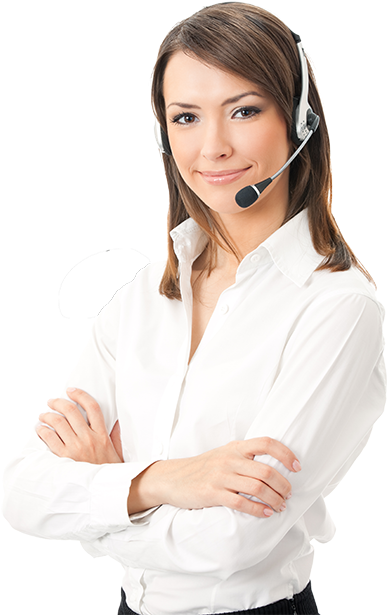