Table of Contents
Introduction
The global Functionally Graded Materials (FGM) market is witnessing steady growth, with its size projected to reach approximately USD 1.7 billion by 2034, up from USD 1.1 billion in 2024, growing at a (CAGR) of 4.2% during the forecast period from 2023 to 2033. FGMs are advanced materials that have a gradual variation in composition or microstructure over their volume, making them ideal for applications in industries such as aerospace, automotive, healthcare, and electronics.
The growing demand for high-performance materials with enhanced durability, resistance to heat, and customized mechanical properties is a key factor driving the market’s expansion. Additionally, advancements in additive manufacturing technologies, which allow for precise control over material properties, are boosting the adoption of FGMs in sectors like aerospace and biomedical engineering.
However, challenges such as high production costs, limited material availability, and complex manufacturing processes remain hurdles for widespread commercialization. Recent developments in the FGM market have focused on overcoming these obstacles, with companies investing in research and development to reduce production costs and improve material efficiency.
For instance, the use of 3D printing techniques for FGM production is gaining traction, enabling more cost-effective and customized solutions. Furthermore, the increasing need for lightweight, high-strength materials in the aerospace and automotive industries is expected to further fuel market growth. Despite these opportunities, the FGM market faces competition from traditional materials and the need for further standardization and quality control in production processes.
Key Takeaways
- The Global Functionally Graded Materials (FGM) Market is expected to be worth around USD 1.7 Billion by 2034, up from USD 1.1 Billion in 2024, and grow at a CAGR of 4.2% from 2025 to 2034.
- Ceramics-based FGMs dominate the market, accounting for a 42.3% share globally.
- The aerospace and defense sector leads with a 38.1% share in the FGMs market.
- North America Holds 32.4% Share of Functionally Graded Materials (FGM) Market, USD 0.3 Bn.
Report Scope
Report Features | Description |
---|---|
Market Value (2024) | USD 1.1 Billion |
Forecast Revenue (2034) | USD 1.7 Billion |
CAGR (2025-2034) | 4.2% |
Segments Covered | By Material Type (Ceramics-Based FGM, Metal-Based FGM, Polymer-Based FGM, Composite-Based FGM, Others), By End-Use Industry (Aerospace and Defense, Automotive, Healthcare, Energy, Electronics, Industrial Manufacturing, Others) |
Competitive Landscape | 3M, Alcoa Corporation, Arconic, Boeing, CeramTec, Corning Incorporated, General Electric (GE), Hitachi Metals, Ltd., Honeywell International Inc., Kyocera Corporation, NASA,, Raytheon Technologies, Siemens AG, Sumitomo Electric Industries, Ltd., Toshiba |
Emerging Trends
- Increasing Use of 3D Printing for FGM Production One of the most significant emerging trends in the FGM market is the growing adoption of 3D printing or additive manufacturing technologies. This innovation allows for the precise control of material composition and microstructure, enabling the production of FGMs with complex geometries and tailored properties. In 2024, the use of 3D printing for FGM applications is expected to contribute to a 15% increase in market adoption, particularly in industries like aerospace and medical implants.
- Growth in Aerospace and Automotive Applications The aerospace and automotive industries are increasingly turning to FGMs for lightweight, high-performance components. These industries demand materials that offer superior heat resistance, strength, and durability. FGMs’ ability to combine different material properties in a single component makes them ideal for such applications. The demand for FGMs in aerospace, driven by the need for components that can withstand high temperatures and stress while remaining lightweight. As of 2024, FGMs are being used in components like turbine blades and exhaust systems, areas where traditional materials have limitations.
- Development of Biomedical Applications In the biomedical sector, FGMs are gaining popularity for use in implants and prosthetics due to their ability to closely mimic the mechanical properties of bone and tissue. The trend towards personalized medicine is driving the demand for FGMs in medical applications. FGMs can be designed to have gradients in mechanical properties that align with the body’s natural structures, improving the longevity and comfort of implants.
- Advances in Metal Matrix FGMs Metal matrix functionally graded materials (MMFGMs) are becoming increasingly important due to their enhanced mechanical properties, such as high strength, wear resistance, and heat resistance. These materials are particularly suited for high-stress applications in industries like automotive and energy. The development of MMFGMs has been aided by advancements in metal processing technologies, such as powder metallurgy and casting. The demand for MMFGMs is expected to rise by 7% annually through 2030, particularly in the production of engine parts, aerospace components, and tools.
- Sustainability and Eco-Friendly Production Techniques Sustainability is an emerging trend in the FGM market, with companies exploring environmentally friendly production methods. For example, the development of FGMs from recycled materials or low-energy processes is gaining traction. With increasing pressure from regulatory bodies to reduce carbon footprints, manufacturers are focusing on reducing the environmental impact of FGM production.
Use Cases
- Aerospace Applications Functionally Graded Materials (FGMs) are increasingly used in aerospace for components that need to withstand extreme conditions, such as high temperatures, mechanical stress, and thermal fatigue. For instance, FGM turbine blades and heat shields are designed to resist high thermal gradients and improve overall efficiency. A key advantage of FGMs is that they can gradually transition between materials with different thermal and mechanical properties, ensuring that the materials can withstand both high heat and mechanical loads.
- Biomedical Implants FGMs have significant potential in the biomedical field, particularly in the development of implants and prosthetics. Their ability to simulate the gradient properties of natural bone makes them ideal for applications like orthopedic implants and dental prosthetics. FGMs can provide a seamless transition between different materials, improving the bio-compatibility and longevity of implants. For example, in bone implants, the FGM design allows the implant to mimic the mechanical properties of bone, reducing the risk of implant failure.
- Automotive Parts In the automotive industry, FGMs are used to produce parts that require a combination of lightweight materials with high strength and wear resistance. Components like brake discs, engine parts, and exhaust systems benefit from the tailored properties of FGMs. By incorporating materials with high heat resistance in specific regions, FGMs help reduce the overall weight of vehicles while maintaining durability and performance. The automotive FGM market is expected to grow at 5.1% CAGR by 2030, as manufacturers increasingly seek materials that improve fuel efficiency and safety while reducing environmental impact.
- Energy Sector – Thermal Power Plants The energy sector is another key area where FGMs are gaining traction, particularly in high-temperature environments such as thermal power plants. FGMs are used in parts like turbine blades and heat exchangers, where they offer superior thermal stability and resistance to thermal shock. These materials help improve the overall efficiency of power generation while reducing the maintenance costs of critical components.
- Electronic Devices Functionally Graded Materials are also being explored in the electronics industry, where their ability to manage heat dissipation and electrical conductivity is crucial. In semiconductor applications, FGMs are used to manage heat between components, preventing overheating and improving the overall lifespan of electronic devices. The use of FGMs in electronics is expected to grow as consumer demand for smaller, more powerful, and longer-lasting electronic devices increases.
- Marine Applications FGMs are also increasingly utilized in the marine sector, particularly for components like ship hulls and marine turbines, where materials must withstand corrosion, high stress, and harsh environmental conditions. FGMs offer significant advantages by combining materials with excellent corrosion resistance in certain parts of the structure, while still providing strength and toughness where needed.
Major Challenges
- High Production Costs One of the biggest challenges in the Functionally Graded Materials (FGM) market is the high cost of production. The manufacturing process of FGMs is complex and often requires advanced techniques such as additive manufacturing, powder metallurgy, or laser cladding. These processes can be expensive due to the need for specialized equipment and materials. As of 2024, the production cost of FGMs is about 30-40% higher than that of traditional materials used in similar applications, such as alloys and composites.
- Manufacturing Complexity and Scalability The manufacturing of FGMs requires precise control over the material composition gradient and microstructure across the material’s volume. This requires advanced techniques like powder deposition or selective laser melting, which are not yet fully standardized across industries. In 2024, only 15-20% of FGM production facilities have the capability to handle large-scale production with consistent quality. Scaling up these processes while maintaining precision and reducing defect rates remains a major challenge. As a result, many companies in the FGM market face limitations in their ability to meet large-volume demand, especially in industries like aerospace and automotive, where high-performance materials are required in mass production.
- Material Availability and Supply Chain Issues The availability of raw materials for FGM production is another critical challenge. FGMs require specific combinations of materials, including metals, ceramics, and polymers, which are not always readily available in the precise forms needed for the manufacturing process. Supply chain disruptions, as seen during the COVID-19 pandemic, can further complicate this issue, causing delays in production timelines. In 2024, the supply chain for certain high-performance materials needed for FGM production, such as titanium alloys, remains tight, leading to 5-7% increases in material costs.
- Limited Standardization and Regulatory Challenges The lack of standardization in FGM production processes and materials poses a challenge for the widespread adoption of FGMs across industries. Each FGM product can be highly customized, which makes it difficult to establish universally accepted standards for quality, performance, and safety. This lack of standardization also extends to the testing and certification processes, which vary by region and application. For example, in the aerospace and medical industries, regulatory approvals for FGMs can take several years due to the complexity of demonstrating their safety and performance under extreme conditions.
- Performance Uncertainty in Long-Term Applications While FGMs show great potential for high-performance applications, their long-term performance under real-world conditions is still not fully understood. For example, the durability of FGM components in aerospace or automotive environments, where they are subjected to high stress, extreme temperatures, and corrosion, is still a subject of ongoing research. The uncertainty surrounding their long-term performance could lead to reluctance in adopting FGMs in critical applications. A Frost & Sullivan (2023) survey indicated that 27% of companies in the aerospace sector are hesitant to adopt FGMs due to concerns about their performance under extreme conditions and the lack of long-term data.
- Competition from Conventional Materials Despite the advantages of FGMs, they face stiff competition from conventional materials such as composites, ceramics, and metals. In many industries, these traditional materials have a well-established track record of performance and lower costs. For example, in the automotive sector, companies are more likely to use carbon fiber composites or aluminum alloys for structural components due to their lower cost and proven reliability.
Market Growth Opportunities
- Rising Demand in Aerospace and Defense The aerospace and defense industries represent a significant opportunity for the growth of Functionally Graded Materials (FGMs). With the increasing demand for lighter, stronger, and more heat-resistant components, FGMs are well-positioned to meet these needs. The use of FGMs in turbine blades, heat shields, and exhaust systems is expected to grow substantially. The global aerospace sector is projected to grow at a CAGR of 4.6% from 2024 to 2032, and FGMs are poised to capture a larger market share as the industry increasingly demands high-performance materials that can withstand extreme conditions.
- Expanding Medical Applications Functionally Graded Materials have significant potential in the medical field, especially in orthopedic and dental implants. As the global population ages, the demand for high-quality medical implants that can integrate seamlessly with natural bone tissue is growing. FGMs can be designed with specific gradients in mechanical properties, making them ideal for improving the longevity and comfort of implants.
- Technological Advancements in Additive Manufacturing The development of additive manufacturing (3D printing) technologies offers significant opportunities for the production of FGMs. Additive manufacturing allows for greater control over material properties, enabling the creation of complex geometries and precise gradients in materials. The market for 3D printing of FGMs is growing rapidly, with adoption expected to increase by 15% annually from 2024 to 2030. According to a report by Frost & Sullivan (2023), this technology will enable manufacturers to reduce production costs, make FGMs more accessible to different industries, and accelerate their adoption in industries like aerospace, automotive, and biomedical engineering.
- Growth in Automotive Sector (Lightweighting) As automakers shift toward electric vehicles (EVs) and strive to meet regulatory standards for fuel efficiency, there is a growing demand for lightweight, durable materials. Functionally Graded Materials offer a unique advantage in this area by combining lightweight structures with high strength and wear resistance. The automotive sector is expected to see significant adoption of FGMs, particularly in high-performance components such as engine parts, brake systems, and structural components. The global automotive FGM market is forecast to grow at a CAGR of 5.1% through 2030, driven by the push for lightweight vehicles and the growing demand for sustainable manufacturing practices.
- Energy Sector and Advanced Power Systems The energy sector offers promising growth opportunities for FGMs, particularly in high-temperature applications like thermal power plants, nuclear reactors, and renewable energy technologies. FGMs are being used in components such as turbine blades and heat exchangers, where their ability to withstand extreme heat and thermal shock is critical. As global energy consumption rises, the demand for more efficient, durable, and sustainable materials in power generation systems will continue to grow.
- Emerging Markets Adoption Emerging markets, particularly in Asia-Pacific and Latin America, are poised to become a significant source of growth for FGMs. As countries in these regions industrialize and their manufacturing sectors expand, there is an increasing demand for advanced materials that offer enhanced performance. The growing automotive, aerospace, and energy industries in these regions present a substantial opportunity for FGMs. In Asia-Pacific, for example, the demand for FGMs in automotive applications is expected to grow at 8% annually due to the rapid expansion of electric vehicle production and infrastructure.
Top Key Players in the Market
- 3M
- Alcoa Corporation
- Arconic
- Boeing
- CeramTec
- Corning Incorporated
- General Electric (GE)
- Hitachi Metals, Ltd.
- Honeywell International Inc.
- Kyocera Corporation
- NASA,
- Raytheon Technologies
- Siemens AG
- Sumitomo Electric Industries, Ltd.
- Toshiba
Recent Developments
In 2024, 3M is focusing on improving FGM manufacturing processes, particularly in the aerospace, automotive, and electronics sectors, by utilizing its extensive knowledge in coatings and adhesives. For example, 3M’s collaboration with aerospace giants to develop FGMs for turbine engine applications has led to prototypes expected to enter commercial use by 2025. In terms of financial impact, 3M’s materials division, which includes its work in FGM, generated USD 7.5 billion in revenue in 2023, with expectations for this segment to grow by 5% annually over the next five years.
In 2023, Alcoa’s total revenue from its advanced materials division, which includes FGMs, reached USD 13.2 billion, with the FGM segment forecast to grow by 6% annually over the next five years. The company’s focus on sustainable materials and energy-efficient production methods is also contributing to its growth in the FGM market, as industries increasingly demand environmentally friendly and durable solutions. With its strong foundation in metal manufacturing and ongoing investments in material science, Alcoa is well-positioned to capitalize on the expanding FGM market.
In 2024, Arconic is focusing on expanding its portfolio of high-performance alloys, leveraging its expertise in additive manufacturing and precision casting to produce FGMs that offer superior strength, thermal resistance, and lightweight properties. The company is particularly focused on using FGMs in applications like turbine blades, heat exchangers, and lightweight structural components for aerospace. Arconic’s partnership with major aerospace manufacturers to design and produce FGM components is expected to generate significant revenue growth, with the FGM market share for Arconic projected to grow by 7% annually from 2024 to 2030.
In 2024, Boeing is focusing on utilizing FGMs for critical components such as turbine blades, heat shields, and other high-stress parts used in both commercial and military aircraft. The company is exploring FGM applications to improve durability, reduce weight, and increase resistance to extreme temperatures, which are crucial in aerospace. Boeing’s R&D efforts in collaboration with materials scientists have led to promising advancements in 3D printing and additive manufacturing techniques for producing FGMs, enabling more cost-effective production of complex aerospace parts.
In 2024, CeramTec is expanding its use of FGMs in high-performance applications, particularly in components like turbine blades, cutting tools, and implants. The company leverages its expertise in ceramics to create FGMs with varying properties, such as improved strength, wear resistance, and thermal stability, to meet the demanding requirements of these sectors.
In 2024, Corning is focusing on advancing the development of FGMs that combine its expertise in glass with other materials to create products with customized properties, such as increased strength, improved thermal resistance, and enhanced optical characteristics. The company’s work in FGM applications includes the development of next-generation materials for sensors, displays, and advanced automotive components.
In 2024, GE is focusing on leveraging FGMs in its gas turbine and aircraft engine components, where combining materials with different properties, such as heat resistance and strength, is crucial for performance. GE’s innovations in FGM are expected to significantly enhance the efficiency, durability, and safety of its turbine blades and other critical aerospace components.
In 2024, Honeywell is focusing on using FGMs to improve the performance of its aerospace components, such as turbine blades and heat exchangers, by creating materials that combine both strength and thermal resistance. The company’s work in FGMs also extends to its energy solutions, where customized material properties are crucial for high-efficiency equipment.
In 2024, Kyocera is focusing on the development of FGMs that integrate ceramic and metal materials to create components with enhanced mechanical, thermal, and electrical properties. This work is especially crucial in industries like automotive, where lightweight, high-strength materials are needed to improve fuel efficiency and performance. Kyocera’s research into FGMs is also being applied in the production of sensors and high-performance parts for aerospace applications.
In 2024, NASA is focusing on FGMs to enhance the durability, thermal resistance, and lightweight properties of components used in rocket engines, spacecraft heat shields, and other critical space technology. The agency’s work on FGMs aims to create materials that can withstand the extreme conditions of space travel, including high temperatures and mechanical stress. NASA’s FGM research is being conducted in collaboration with leading universities and material science companies, with a particular focus on additive manufacturing techniques to produce complex FGM structures more efficiently.
In 2024, the company is focusing on utilizing FGMs to improve the performance of components such as turbine blades, heat shields, and sensors, which require high levels of thermal resistance, strength, and durability. Raytheon’s FGM research is geared towards developing materials that can withstand extreme environments, like those found in missile systems and spacecraft.
In 2024, Siemens is focused on advancing FGMs for use in energy-efficient turbines, high-performance motors, and components for electric vehicles. The company is leveraging FGMs to develop parts with superior thermal and mechanical properties, helping improve efficiency and reduce energy consumption in its products.
Conclusion
In conclusion, the Functionally Graded Materials (FGM) market is poised for steady growth, driven by advancements in manufacturing technologies, increasing demand for high-performance materials across various industries, and the rise of applications that require tailored material properties. However, challenges such as high production costs, manufacturing complexities, and material availability continue to pose barriers to broader adoption. Despite these hurdles, opportunities abound in emerging markets, the push for sustainability, and the growth of additive manufacturing, which is expected to make FGM production more cost-effective and scalable. As industries increasingly seek lightweight, durable, and energy-efficient materials, FGMs will continue to be a critical part of the material innovation landscape. The key to accelerating their adoption will be addressing current production challenges and capitalizing on technological advancements to unlock the full potential of FGMs.
Discuss Your Needs With Our Analyst
Please share your requirements with more details so our analyst can check if they can solve your problem(s)
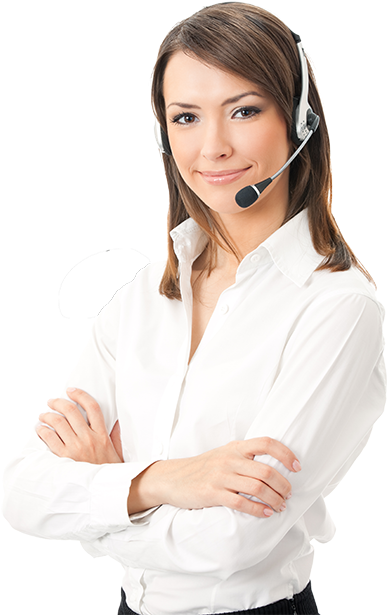