Table of Contents
Introduction
The Global Automotive Silicone Market is projected to reach a value of USD 621.4 million by 2033, up from USD 440.5 million in 2023, with a compound annual growth rate (CAGR) of 3.5% over the forecast period from 2024 to 2033.
The automotive silicone market refers to the segment of the automotive industry focused on the production and use of silicone-based materials in various automotive applications. Silicones are synthetic polymers known for their thermal stability, flexibility, durability, and resistance to extreme temperatures, making them critical components in the manufacturing of automotive parts.
These materials are used in a wide range of applications, including sealing, gasketing, insulation, and coatings, particularly in engine components, electrical systems, and exterior/interior trims.
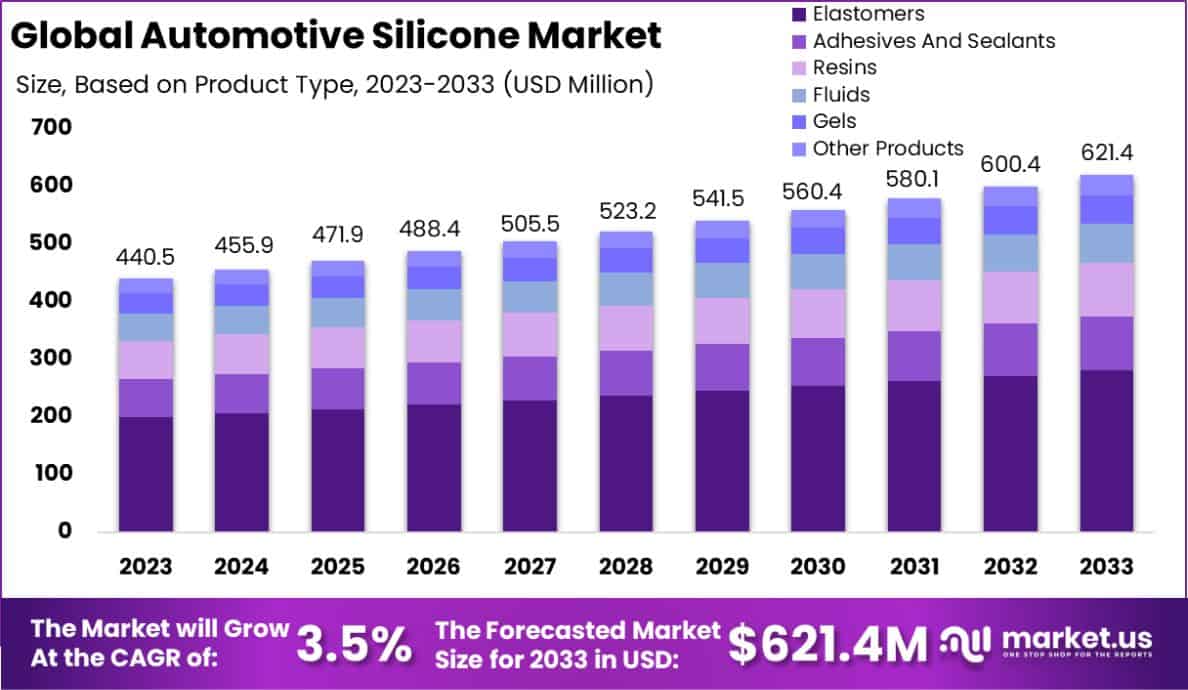
Several key growth drivers are influencing the expansion of the automotive silicone market. One of the primary factors is the increasing demand for lightweight materials to improve fuel efficiency and reduce emissions in compliance with global environmental regulations. Silicones contribute to vehicle weight reduction by replacing heavier materials without compromising on performance.
Additionally, the growing trend towards electric vehicles (EVs) has further accelerated the demand for silicone-based products, as they are essential for thermal management and insulating electric components. Moreover, advancements in automotive technology, such as autonomous driving and enhanced safety features, require high-performance materials like silicones to ensure reliability and functionality in critical systems.
The automotive silicone is driven by the automotive industry’s shift towards sustainability and innovation. As automakers focus on producing greener vehicles, including electric and hybrid models, the need for silicone materials increases due to their application in battery technology, thermal insulation, and weather-resistant components.
Furthermore, consumers’ preference for enhanced vehicle aesthetics and comfort, such as smoother finishes and improved sealing systems, also contributes to the rising demand for silicone-based materials in both the interior and exterior of vehicles. The global push towards stricter emission standards, particularly in Europe, North America, and China, has bolstered the market by promoting the use of materials that enhance vehicle efficiency.
There are several promising opportunities for growth in the automotive silicone market. As electric vehicles (EVs) continue to gain traction worldwide, the market for silicone in thermal management systems, charging stations, and battery protection solutions is expected to surge. The growing adoption of autonomous and connected vehicles also presents an opportunity, as these technologies require highly reliable and durable materials for sensors, cameras, and other electronic components.
Furthermore, as developing markets in Asia-Pacific, Latin America, and Eastern Europe continue to expand their automotive sectors, they offer untapped potential for silicone manufacturers, especially as these regions adopt stricter environmental regulations and move towards electrification. Additionally, ongoing research and development in advanced silicone formulations, such as bio-based silicones, could open new avenues for sustainable growth in the market.
Key Takeaways
- The global automotive silicone market is expected to reach USD 621.4 million by 2033, up from USD 440.5 million in 2023, growing at a CAGR of 3.5% from 2024 to 2033.
- In 2023, elastomers held the dominant position in the product type segment, capturing a 45.3% share of the market.
- The interior and exterior parts application segment led the market in 2023, accounting for 38.3% of total share.
- The Asia Pacific region was the largest market in 2023, with a 45.3% share, generating USD 199.5 million in revenue.
Automotive Silicone Statistics
- Electric vehicles are expected to use 20% more silicone than traditional internal combustion vehicles.
- High-temperature silicone products can withstand up to 300°C (572°F) in automotive applications.
- Silicone-based adhesives offer bond strengths of up to 3.5 MPa (508 psi).
- Modern cars contain 50-100 silicone seals and gaskets on average.
- Automotive-grade silicone rubbers have a Shore A hardness range of 30 to 80.
- Silicone’s dielectric strength ranges from 15-25 kV/mm, making it ideal for electrical insulation.
- Silicone’s low compression set (typically <25%) makes it suitable for gaskets and seals.
- Silicone maintains properties in temperatures from –55°C to 200°C (-67°F to 392°F).
- Some automotive silicone products last over 10 years under normal conditions.
- Silicone’s low surface tension (20-25 mN/m) contributes to its water-repellent properties.
- Thermal conductivity of automotive silicone ranges from 0.1 to 1.5 W/mK.
- Silicone products can have an elongation at break of up to 1000%, offering flexibility.
- Silicone’s coefficient of thermal expansion is around 2-4 x 10^-4 /°C, ensuring stability.
- Some silicone formulations withstand over 1000 hours of exposure to automotive fluids.
- Silicone’s acoustic damping properties reduce vehicle noise and vibration by up to 15%.
- Using silicone can reduce component weight by up to 50% compared to traditional rubber parts.
- Silicone-based coatings improve scratch resistance by up to 60%.
- Automotive silicone products have tensile strengths up to 10 MPa (1450 psi).
- Silicone’s refractive index (1.4-1.5) suits optical applications in automotive lighting.
- Silicone’s gas permeability is 10 times higher than natural rubber, useful for seals.
- Silicone’s volume resistivity exceeds 10^15 ohm-cm, offering excellent electrical insulation.
- Some silicone products endure over 1 million flex cycles without failure.
- Silicone-based thermal interface materials can reduce automotive electronics temperatures by 20°C.
- Silicone’s low VOC content (<0.5%) supports automotive sustainability goals.
- Some silicone products maintain over 90% of properties after 1000 hours of heat aging at 150°C.
- Silicone’s hydrophobicity results in water contact angles over 100°, useful for coatings.
- Silicone in weather stripping improves energy efficiency by reducing air leakage by 30%.
- Some silicone elastomers have a tear strength exceeding 40 kN/m.
- Silicone resists fungal growth, with zero growth in ASTM G21 tests, suitable for HVAC systems.
- Silicone products can function over a temperature range of 250°C.
- Some silicone adhesives can bond materials with up to 300% thermal expansion mismatch.
- Silicone remains stable after extended exposure to temperatures above 150°C.
- Using silicone in automotive parts can extend component lifespan by up to 25%.
- Some silicone products have a shelf life of over 12 months with proper storage.
- Silicone maintains over 50% of its properties after 10,000 hours at 150°C.
- Automotive silicone products have a density range of 1.1 to 1.5 g/cm³, contributing to lightweight design.
- Some silicone elastomers can recover up to 99% of their original shape after compression.
- Using silicone in paint applications can improve scratch resistance by up to 300%.
- Silicone’s temperature resistance is effective up to 200°C (392°F).
- The silicone adhesives market is projected to grow by over 5% annually through 2025.
- Major players invest over $300 million annually in R&D for silicone technologies.
- By 2030, over 50% of new vehicles are expected to feature ADAS systems.
- Silicone can stretch up to 800% without breaking.
- Silicone demand for EVs is projected to increase by over 40% by 2025.
- The automotive silicone industry contributes over $1 billion annually in job creation and manufacturing.
- Top companies invested over $150 million in silicone technologies in 2023.
- 65% of consumers prioritize vehicle durability and performance, boosting silicone adoption.
- Silicone typically lasts over 15 years in automotive applications without degradation.
- Approximately 20% of automotive components now utilize silicone in modern vehicles.
- 27%: Silicon constitutes over 27% of Earth’s crust by mass.
- 8th most abundant element: Silicon is the 8th most abundant element in the universe, at 650 parts per million.
- 92.23%: Silicon-28 makes up 92.23% of natural silicon.
- 170 years: Silicon-32, a radioisotope, has a half-life of 170 years.
- 15 mg/m³: OSHA’s legal limit for total workplace silicon exposure is 15 mg/m³ over an 8-hour workday.
- 5 mg/m³: OSHA’s limit for respiratory silicon exposure is 5 mg/m³.
- 99.9%: Silicon is obtained at >99.9% purity for use in semiconductors.
- 99.9999%: Polysilicon purity reaches 99.9999% in semiconductor production using the Siemens process.
Emerging Trends
- Increasing Role in Electric Vehicles (EVs) The transition to electric vehicles is significantly boosting the demand for silicone. Silicones are essential in EVs for battery insulation, thermal management, and sealing components, helping improve battery life and performance. As EV production ramps up globally, the use of silicone in electric drivetrains and high-voltage cables is becoming more prevalent.
- Lightweighting for Fuel Efficiency Automotive manufacturers are increasingly turning to lightweight materials like silicone to reduce vehicle weight and enhance fuel efficiency. Silicones, due to their strength and flexibility, are replacing heavier materials in components like gaskets, seals, and engine parts, contributing to better fuel economy and lower emissions.
- Advancements in Sustainable Silicone Solutions There is a growing trend toward the development of bio-based and recyclable silicones to address environmental concerns. These sustainable silicones help reduce dependency on petroleum-based materials, making the automotive supply chain more eco-friendly. This aligns with the global push towards greener manufacturing processes.
- Adoption of Silicone in Autonomous Vehicles As the market for autonomous and connected vehicles expands, silicones are being increasingly used in advanced sensors, cameras, and other electronic components that require durability and stability under varying conditions. Silicone’s high heat resistance and insulating properties make it ideal for these critical applications.
- 3D Printing and Customization Silicone is being integrated into 3D printing technologies, allowing for the production of customized automotive components. This innovation enables manufacturers to create complex parts with enhanced performance properties, contributing to more flexible and efficient production processes
Top Use Cases
- Thermal Management in Electric Vehicles (EVs) Silicone is extensively used in EV battery packs for thermal insulation and management, preventing overheating and enhancing battery life. As the electric vehicle market grows at a CAGR of over 20%, the demand for silicone materials in these applications is projected to rise, particularly in high-voltage components.
- Engine Gaskets and Seals Silicone’s ability to withstand extreme temperatures makes it ideal for use in engine gaskets, seals, and hoses. These components are crucial for maintaining engine efficiency and reducing emissions, a growing focus as global emission regulations tighten.
- Interior and Exterior Parts Silicone materials are commonly used in weatherproofing, trims, and coatings for vehicle interiors and exteriors. These materials not only improve aesthetic appeal but also provide UV resistance and durability.
- Electrical System Insulation In modern vehicles, especially electric and hybrid models, electrical insulation is vital. Silicone is used in wiring harnesses, connectors, and ignition cables due to its excellent dielectric properties and resistance to heat, ensuring safety and performance under high-voltage conditions.
- Airbag Coatings Silicone-coated airbags are essential for maintaining flexibility and durability in a critical safety component. The material’s ability to endure high pressures and deploy reliably makes it a key choice in the growing demand for automotive safety features, contributing to the wider adoption of silicone in vehicles
Major Challenges
- Volatility in Raw Material Prices The automotive silicone market is highly dependent on raw materials like silicon and hydrocarbons, both of which are subject to price fluctuations. These fluctuations, driven by global supply chain disruptions or geopolitical tensions, directly impact the production costs of silicone products. The increased cost of raw materials can hinder profitability for manufacturers and lead to higher prices for end-users.
- Environmental Regulations and Sustainability Concerns As sustainability becomes a priority, the silicone industry faces mounting pressure to reduce its environmental footprint. The production of silicone involves significant energy use and emissions, prompting stricter regulations. Automotive manufacturers are also seeking bio-based or recyclable silicone alternatives, but scaling up these sustainable options poses technological and financial challenges.
- High Production Costs Compared to alternative materials, silicone production is more expensive due to the energy-intensive processes involved and the complexity of refining raw silicon. This high cost can be a barrier for widespread adoption, particularly in cost-sensitive automotive markets like mass-produced passenger cars.
- Competition from Alternative Materials Automotive manufacturers are continuously exploring alternatives such as thermoplastics and elastomers that can perform similar functions at a lower cost. While silicones offer superior performance in certain areas, alternatives with lower price points may be preferred for non-critical applications, creating competition for silicone products.
- Limited Recycling and Disposal Options Silicones are not easily recyclable, which is a growing issue as industries move toward circular economies. The limited availability of recycling solutions for silicone-based products could become a bottleneck as regulatory frameworks increasingly favor recyclable or biodegradable materials in the automotive secto
Top Opportunities
- Rising Demand for Electric Vehicles (EVs) The accelerating shift toward electric vehicles offers a significant growth opportunity for automotive silicone, particularly in battery insulation, thermal management, and sealing applications. As the EV market grows at a CAGR exceeding 20%, the use of silicone for heat resistance and electrical insulation will be critical for enhancing battery safety and lifespan.
- Expansion of Lightweighting Initiatives With stricter fuel efficiency and emissions regulations, automakers are increasingly seeking lightweight materials to reduce vehicle weight. Silicone’s high strength-to-weight ratio makes it a preferred choice for components like gaskets, seals, and hoses. This shift towards lightweight materials could boost silicone’s use in various automotive applications, particularly as manufacturers aim to meet global CO2 reduction targets.
- Growth in Autonomous and Connected Vehicles The adoption of autonomous and connected vehicle technologies presents a new opportunity for silicone materials. These vehicles rely on advanced sensors, cameras, and electronic components, all of which require durable, heat-resistant materials like silicone for protection and insulation. The global autonomous vehicle market is expected to grow significantly in the next decade, driving the demand for high-performance materials.
- Increased Focus on Sustainability As the industry moves towards eco-friendly solutions, there is an opportunity to develop and commercialize bio-based or recyclable silicones. Innovations in sustainable silicone production can open new doors in regions where environmental regulations are becoming stricter, particularly in Europe and North America, offering a competitive advantage to manufacturers who prioritize green technologies.
- Aftermarket and Maintenance Services The aftermarket segment, including replacement parts for gaskets, seals, and hoses, presents ongoing opportunities as vehicles require regular maintenance. The durable nature of silicone products extends the lifespan of components, making it an ideal material for aftermarket products. This growing demand for replacement parts and vehicle repairs offers a consistent revenue stream for silicone manufacturers
Key Player Analysis
- Dow Inc. Dow is a global leader in the silicone market, offering a wide range of automotive solutions, including adhesives, sealants, and elastomers. Their silicone products are heavily utilized in thermal management systems and electrical components for electric vehicles (EVs), which is crucial as the EV market grows rapidly. Dow’s commitment to sustainability and innovation, such as recyclable silicones, helps strengthen its position in the automotive industry.
- Wacker Chemie AG Wacker Chemie is another major player, known for its high-performance silicone products used in both internal combustion engine (ICE) vehicles and electric vehicles. The company specializes in elastomers and fluids, which are used in automotive gaskets, seals, and thermal insulation. Wacker’s strong R&D investments and global presence, especially in Europe and Asia-Pacific, give it a competitive edge.
- Elkem ASA Based in Norway, Elkem ASA is a significant player in the global silicone market, offering specialized automotive-grade silicones. The company focuses on lightweight materials for automotive components, which help improve fuel efficiency and reduce emissions. Elkem is expanding its footprint in Asia, especially in the electric vehicle sector, and continues to grow its market share through strategic acquisitions and partnerships.
- Henkel AG & Co. KGaA Henkel is a leader in adhesives and sealants, providing advanced silicone-based solutions that enhance vehicle performance, durability, and safety. Their silicone materials are critical for bonding and sealing in both conventional and electric vehicles. Henkel’s automotive business is particularly strong in Europe and North America, benefiting from the growing demand for lightweighting and sustainability.
- Shin-Etsu Chemical Co., Ltd. Shin-Etsu, a Japanese company, is a top producer of silicone materials, particularly in the electronics and automotive sectors. Their silicone elastomers and fluids are widely used in EV batteries and electronic components, where thermal stability and electrical insulation are vital. With a strong focus on innovation, Shin-Etsu continues to expand in the Asian market, leveraging its expertise to meet the rising demand for electric and hybrid vehicles
Recent Developments
- In 2022, Dow announced the launch of its SILASTIC™ SA 994X Liquid Silicone Rubber (LSR) series, aiming to support smarter and more sustainable technologies for the mobility and transportation industry.
- In 2024, Elkem’s BLUESIL™ TCS 7538 LE won the SEAL Sustainable Product Award. The award recognizes companies contributing to sustainability and developing innovative solutions with a positive environmental impact.
- In 2024, Wacker Chemie AG began construction on a new production site in Karlovy Vary, Czech Republic. The site will produce high-performance silicones starting in 2025 and silicone rubber by 2028, creating 200 new jobs and supporting key industries like electromobility and medical care.
Conclusion
The automotive silicone market is poised for sustained growth, driven by advancements in vehicle technology, environmental regulations, and the increasing demand for electric vehicles. Silicone’s unique properties, such as heat resistance, durability, and lightweight nature, make it indispensable for modern automotive applications, from thermal management in EVs to sealing and insulating components in both internal combustion and autonomous vehicles.
Despite challenges like fluctuating raw material costs and environmental concerns, opportunities abound in areas like sustainable silicone production, aftermarket demand, and the rising focus on vehicle efficiency. As the automotive industry continues its transformation, silicone will play a vital role in supporting innovation and meeting regulatory standards, positioning it as a critical material for the future of mobility.
Discuss Your Needs With Our Analyst
Please share your requirements with more details so our analyst can check if they can solve your problem(s)
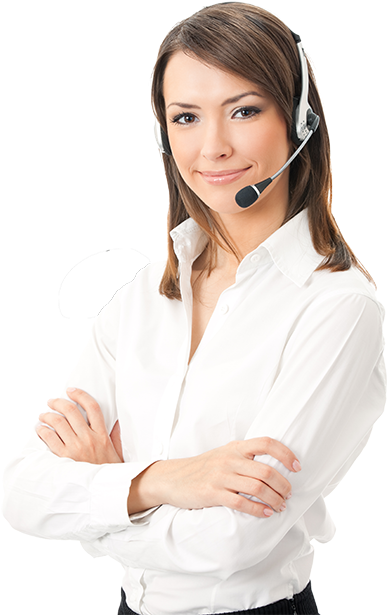