Table of Contents
Introduction
The Global Abrasive Blasting Equipment Market is projected to reach USD 901.0 million by 2033, up from USD 547.9 million in 2023, growing at a compound annual growth rate (CAGR) of 5.10% from 2024 to 2033.
Abrasive blasting equipment refers to machinery used in the process of cleaning, smoothing, or preparing surfaces through the high-pressure projection of abrasive materials like sand, steel grit, or glass beads. This equipment plays a crucial role in industries such as manufacturing, construction, automotive, aerospace, and shipbuilding, where surface preparation is essential for painting, coating, or rust removal. The abrasive blasting equipment market encompasses a wide range of products, including portable blasters, automated systems, and specialized machines designed for specific tasks.
Growth in this market is primarily driven by the increasing demand for surface treatment processes across various industries. As industries scale up and embrace new materials and coatings, the need for efficient, high-performance abrasive blasting equipment rises. Key growth factors also include advancements in automation and robotics, which have increased productivity and precision in abrasive blasting operations. Furthermore, environmental regulations pushing for eco-friendly blasting materials and methods are influencing market dynamics, as manufacturers focus on developing safer and more sustainable solutions.
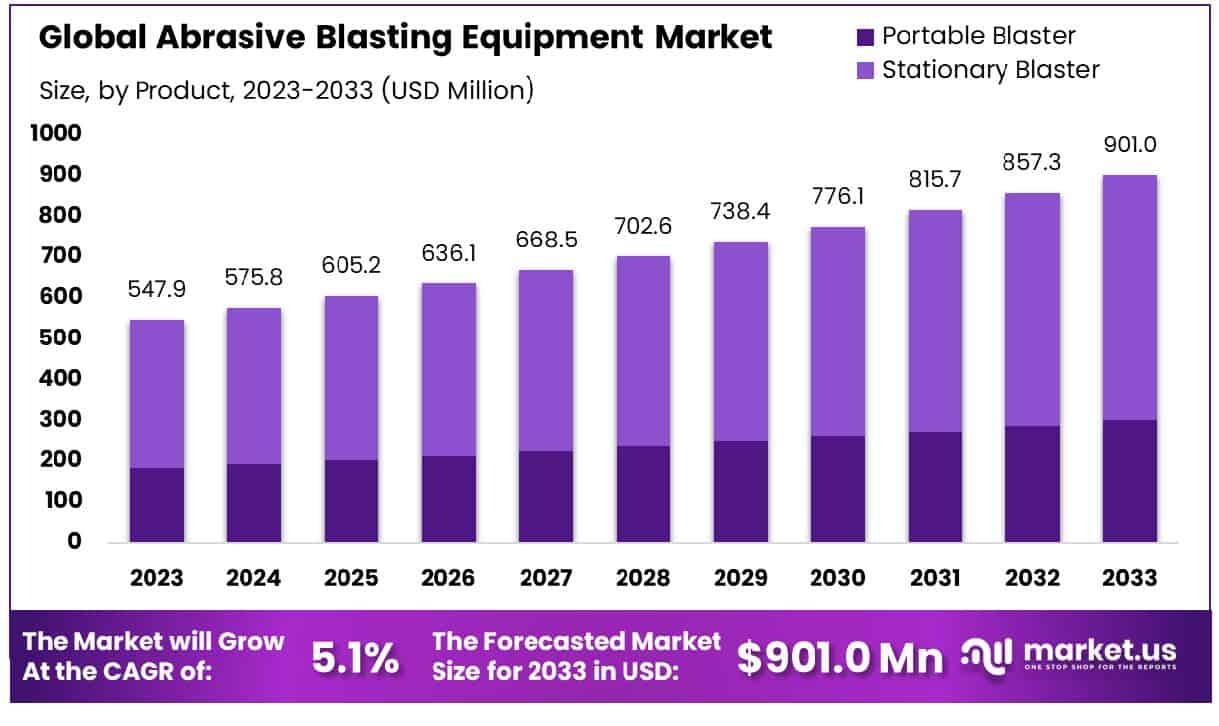
The rise of emerging markets, particularly in Asia-Pacific and Latin America, presents substantial opportunities, as rapid industrialization and infrastructure development drive demand for abrasive blasting services. Additionally, ongoing technological innovations, such as the integration of digital controls and improved abrasive materials, offer potential for market expansion. As industries focus on improving operational efficiency and product quality, the abrasive blasting equipment market is poised for significant growth, providing ample opportunities for both established players and new entrants.
Key Takeaways
- The Abrasive Blasting Equipment Market is expected to reach USD 901.0 Million by 2033, up from USD 547.9 Million in 2023, with a CAGR of 5.10% from 2024 to 2033.
- Asia-Pacific leads the global market, holding a 45.6% share.
- Stationary blasters are the most popular, capturing 64.3% of the market share.
- Automatic operation is preferred in 38.9% of cases, highlighting the trend towards efficiency.
- Dry blasting is the dominant method, making up 60.4% of the market due to its versatility.
- The construction industry is the largest consumer, accounting for 28.5% of the demand.
Key Segments Analysis
Stationary Blasters dominate the abrasive blasting equipment market with a 64.3% share in 2023, thanks to their efficiency and ability to handle large-scale operations in heavy industries like shipbuilding and automotive. These systems offer higher power output and larger material capacity, making them ideal for complex blasting tasks. While Portable Blasters have a smaller market share, their mobility and versatility for smaller or remote jobs are growing in demand.
Automatic Operation blasters hold a 38.9% market share, driven by automation technologies that improve precision, reduce labor costs, and increase productivity. Manual and Semi-automatic Operations are less common, with Manual blasters being essential for detailed tasks, while Semi-automatic systems offer a balance between control and automation. Advancements in robotics and IoT are pushing the trend toward fully automated solutions across industries.
Dry Blasting leads the market with a 60.4% share due to its versatility and effectiveness in cleaning and preparing surfaces without water, making it suitable for a wide range of industries. Wet Blasting, though smaller, is preferred in confined spaces where dust control is critical, and it provides a finer finish, making it ideal for sensitive surfaces. Both methods are evolving with technological advancements to meet stricter environmental standards.
The Construction sector holds the largest share (28.5%) of the abrasive blasting market in 2023, as surface preparation is crucial for coating adhesion in building and infrastructure projects. Other key sectors, such as Automotive, Marine, Oil & Gas, and Metal Fabrication, also rely heavily on abrasive blasting for cleaning and preparing surfaces to ensure durability and resistance to harsh conditions. Market growth across these sectors is being fueled by innovation and the need for enhanced efficiency.
Emerging Trends
- Automation Integration: Increasing demand for automated abrasive blasting systems is on the rise, as companies seek efficiency, precision, and reduced labor costs. Automation allows for more consistent blasting outcomes, improving productivity and safety in industries like aerospace and shipbuilding.
- Sustainable Blasting Materials: The focus is shifting toward using eco-friendly, non-toxic, and recyclable abrasives. Companies are gradually moving away from harmful materials like silica sand to alternatives such as glass beads and plastic media, driven by environmental concerns and regulatory pressure.
- Mobile Blasting Units: There is a growing trend toward mobile abrasive blasting units, especially in industries that require on-site work, such as construction and maintenance. These mobile units offer flexibility and can work in diverse environments, reducing downtime for businesses.
- Advanced Control Systems: Newer abrasive blasting equipment comes with advanced control systems that allow operators to precisely adjust parameters like pressure, flow rate, and blast angle, improving overall performance and customization for specific applications.
- Safety Innovations: With an increasing focus on workplace safety, manufacturers are designing equipment with better dust collection systems, ergonomic designs, and safety features to protect operators from the harmful effects of airborne abrasives and ensure compliance with stricter regulations.
Top Use Cases
- Surface Preparation for Coatings: One of the most common uses of abrasive blasting is preparing surfaces for coatings such as paints and primers. The equipment is used to remove rust, old paint, and other contaminants, creating a clean surface that enhances the adhesion of new coatings.
- Rust and Corrosion Removal: Abrasive blasting is extensively used in the automotive and marine industries for removing rust and corrosion from metal surfaces, ensuring longevity and durability of critical components.
- Concrete Surface Cleaning: In construction and infrastructure sectors, abrasive blasting is utilized to clean and profile concrete surfaces before the application of adhesives or protective coatings. It enhances adhesion and prepares surfaces for further treatment.
- Etching and Finishing: In industries such as metalworking and glass manufacturing, abrasive blasting is used for etching logos, patterns, or designs onto materials like glass, stone, and metal. It provides a precise, high-quality finish for aesthetic purposes.
- Restoration of Historical Buildings: Abrasive blasting is used in the restoration of historical buildings to remove layers of dirt, paint, and other pollutants without damaging delicate surfaces. It allows for the preservation of architectural heritage while maintaining structural integrity.
Major Challenges
- Health and Safety Risks: The high-speed abrasive materials can pose serious risks to workers, including respiratory problems and skin injuries. Ensuring proper protective gear and adherence to safety standards remains a challenge in many industries.
- Environmental Impact: While there is a shift toward eco-friendly materials, abrasive blasting can still generate a significant amount of waste, dust, and environmental contamination. Finding sustainable methods to minimize these impacts remains an ongoing challenge.
- High Initial Costs: The upfront cost of high-quality abrasive blasting equipment can be quite expensive, making it difficult for smaller businesses to invest in advanced systems. While these systems offer long-term benefits, the initial cost can be a barrier to entry.
- Regulatory Compliance: Different countries and regions have strict regulations on the materials used in abrasive blasting, such as restrictions on silica sand. Complying with these rules, which vary across jurisdictions, can be complex for global manufacturers and operators.
- Equipment Maintenance and Downtime: Like any heavy machinery, abrasive blasting equipment requires regular maintenance to ensure optimal performance. Unexpected breakdowns or costly repairs can lead to significant downtime, affecting productivity and profits.
Top Opportunities
- Adoption of Eco-Friendly Materials: There is a growing opportunity to develop and supply more sustainable and non-toxic blasting abrasives. As environmental regulations tighten globally, companies that innovate in this space could capture market share by offering safer, green alternatives.
- Growth in Emerging Markets: Developing countries, especially in Asia and Africa, are experiencing rapid industrial growth. As infrastructure projects, automotive manufacturing, and metalworking activities expand, the demand for abrasive blasting equipment is expected to rise significantly.
- Technological Advancements: The integration of IoT (Internet of Things) and smart sensors in abrasive blasting equipment offers opportunities for real-time monitoring, performance analytics, and predictive maintenance, enabling operators to reduce downtime and increase operational efficiency.
- Demand in Aerospace and Automotive Industries: The aerospace and automotive industries require specialized surface preparation and finishing processes, creating opportunities for customized abrasive blasting solutions. These industries are also increasingly turning to automated and robotic systems for efficiency.
- Expansion of Mobile and Portable Solutions: With more industries moving towards mobile solutions, there is a significant opportunity in providing portable abrasive blasting systems for on-site work. These units are particularly beneficial for maintenance projects in construction, manufacturing, and industrial plants.
Key Player Analysis
In 2024 and beyond, the key players in the Global Abrasive Blasting Equipment Market, such as Guyson Corporation, Norton Sandblasting Equipment, and Clemco Industries Corporation, are poised to dominate due to their strong brand presence and innovative product offerings. Companies like Airblast B.V. and Axxiom Manufacturing, Inc. are emphasizing technological advancements in automation and precision to meet evolving industry demands.
Meanwhile, emerging players like Hangzhou Color Powder Coating Equipment Co. and Fratelli Pezza are expanding their market reach with cost-effective solutions tailored to specific regional needs. The competition is intensifying as these companies invest in enhancing product quality, operational efficiency, and customer-centric innovations.
Top Market Key Players
- Guyson Corporation
- Hangzhou Color Powder Coating Equipment Co., Ltd.
- Norton Sandblasting Equipment
- Airblast B.V.
- Axxiom Manufacturing, Inc.
- Hangzhou Huashengtong Machinery Equipment Co., Ltd.
- Surface Blasting Systems, LLC
- Clemco Industries Corporation
- MMLJ, Inc.
- CONIEX SA
- Fratelli Pezza
Regional Analysis
Asia-Pacific – Abrasive Blasting Equipment Market with Largest Market Share of 45.6% in 2023
The Asia-Pacific region holds the largest share of the Abrasive Blasting Equipment market, accounting for 45.6% of the global market in 2023, with a market value of USD 249.8 million. This dominance is attributed to several factors, including rapid industrialization, significant growth in manufacturing and construction activities, and the increasing demand for surface preparation processes in industries such as automotive, aerospace, and shipbuilding. Countries like China, India, Japan, and South Korea are leading contributors to this market growth, with China being a major hub for abrasive blasting equipment demand due to its robust industrial sector and export-oriented economy.
The growth in infrastructure development projects, both private and governmental, has further bolstered the need for efficient abrasive blasting solutions. Moreover, the region is witnessing advancements in technology, with innovations aimed at improving equipment efficiency and reducing operational costs, thus driving the market’s expansion. The Asia-Pacific region is expected to maintain its dominance in the coming years, fueled by continued industrial activities, urbanization, and increasing investment in manufacturing infrastructure.
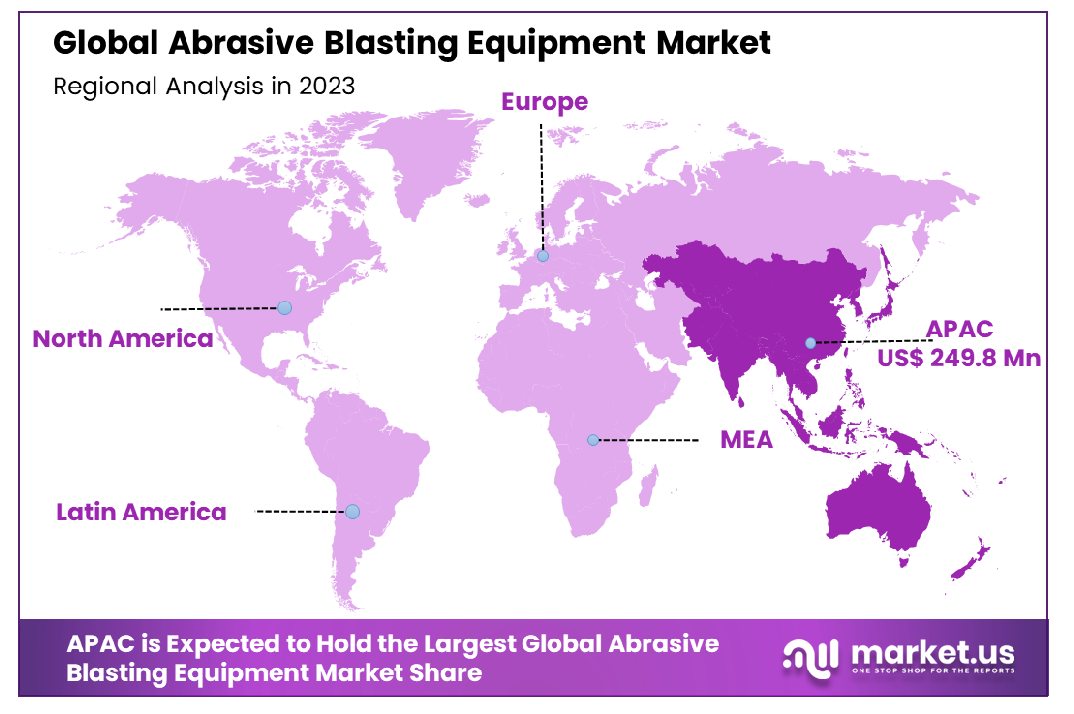
Recent Developments
- In March 2024, Metal Finishing Technologies, LLC (MFT), a prominent provider of metal finishing and coating solutions for the aerospace, defense, and industrial sectors, announced the acquisition of Aqua Blasting Corp., a shot peening and blasting services company based in Bloomfield, CT. This acquisition marks a key step for MFT as part of its partnership with Battle Investment Group, expanding its service offerings and introducing new surface enhancement capabilities to better serve its clients across multiple industries.
- In May 2024, Sherwin-Williams Protective & Marine introduced the Pipeclad Frac-Shun ERC, a groundbreaking erosion-resistant coating designed to protect the interiors of pipes used in fracking. This patent-pending system significantly reduces downtime and maintenance costs while enhancing productivity by offering superior protection against the abrasive effects of sandblasting and grit within pipes, ensuring longer-lasting performance and fewer replacements.
- In September 2024, Graco Inc., a leader in fluid handling technology, unveiled Stellair ACE and Stellair™ industrial air spray guns, the first to earn Ergonomics Performance Certification. Backed by rigorous testing from United States Ergonomics, these spray guns reduce fatigue for industrial painters, increasing efficiency and overall productivity.
- In 2024, industrial sandblasting technology saw a leap forward with innovations that emphasize efficiency and sustainability. Modern sandblasters now deliver higher precision, improved environmental performance, and reduced waste, transforming surface preparation practices across various industries.
Conclusion
The abrasive blasting equipment market is poised for substantial growth, driven by the increasing demand for surface preparation across various industries such as construction, automotive, aerospace, and shipbuilding. Advancements in automation, sustainability, and technological innovations are shaping the future of the market, with a growing preference for eco-friendly materials and efficient, automated systems. While challenges related to health, safety, environmental impact, and high initial costs persist, opportunities in emerging markets, mobile solutions, and the integration of smart technologies are expected to fuel continued market expansion. As industries continue to prioritize surface treatment for product quality, efficiency, and regulatory compliance, the abrasive blasting equipment sector is set for a promising future.
Discuss Your Needs With Our Analyst
Please share your requirements with more details so our analyst can check if they can solve your problem(s)
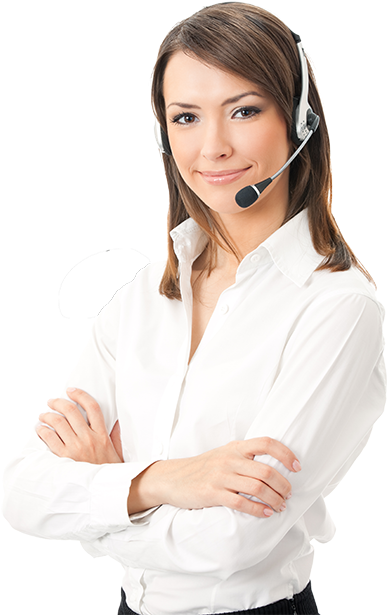