Table of Contents
Introduction
New York, NY – March 24, 2025 – The global market for Rotational Molding Materials is on a steady climb, poised to grow from USD 3,290.7 million in 2024 to an impressive USD 5,763.0 million by 2034, achieving a compound annual growth rate (CAGR) of 5.7%.
This growth is driven by the increasing popularity of rotational molding techniques used in manufacturing various products like large tanks, containers, and recreational items. The method’s ability to produce lightweight, durable, and complex shapes at a low cost boosts its demand across industries such as automotive, construction, and packaging.
The expansion of this market is further fueled by the continuous development of new and improved materials, which open up numerous opportunities for innovation and efficiency. As businesses and consumers increasingly seek cost-effective and high-quality plastic products, the rotational molding materials market is set to expand significantly, offering substantial opportunities for players in the sector.

Key Takeaways
- The global rotational molding materials market was valued at USD 3,290.7 million in 2024.
- The global rotational molding materials market is projected to grow at a CAGR of 5.7% and is estimated to reach USD 5,763.0 million by 2034.
- Among material types, polyethylene accounted for the largest market share of 80.0%.
- Among types, virgin accounted for the majority of the market share at 82.0%.
- Based on forms, powder held the majority of the revenue share at 80.4%.
- Among applications, storage tanks accounted for the largest revenue share of 38.6%.
- Based on end-use, construction held the majority of the revenue share at 24.3%.
- Europe is estimated as the largest market for rotational molding materials with a share of 29.6% of the market share.
➤ For a deeper understanding, click on the sample report link: https://market.us/report/rotational-molding-materials-market/request-sample/
Report Scope
Market Value (2024) | USD 3,290.7 Million |
Forecast Revenue (2034) | USD 5,763.0 Million |
CAGR (2025-2034) | 5.7% |
Segments Covered | By Material Type (Polyethylene, Polycarbonate, Nylon, Polyvinyl Chloride, Polyesters, Polypropylene, and Others), By Type (Virgin, and Recycled), By Form (Powder, and Granules) By Application (Storage Tanks, Automotive Components, Containers, Toys and Leisure, Materials Handling, Industrial, and Others) By End-use (Construction, Automotive, Agriculture, Consumer Goods, Chemical, Food & Beverage, and Others) |
Competitive Landscape | SCG Chemicals, LyondellBasell Industries Holdings B.V., ExxonMobil, Reliance Industries Limited, SABIC, Matrix Polymers Limited, Rototech Industries, GreenAge Industries, Prisma Colour Limited, Petrotech Group, PTT Global Chemical Public Company Limited., DOMO Chemicals, Broadway Colours, Roto Polymers, OSWAL HITECH PVT. LTD., Mabaplast, Kalpataru Polymer Private Limited, Pinaxis Polymer, Xiamen Keyuan Plastic Co.,Ltd, Other Key Players |
➤ Directly purchase a copy of the report – https://market.us/purchase-report/?report_id=142598
Emerging Trends
- Sustainability Initiatives: Companies are increasingly focusing on sustainable practices by using recycled plastics and developing biodegradable materials for rotational molding. This trend is driven by environmental concerns and regulatory pressures, encouraging manufacturers to innovate greener products.
- Advances in Material Science: The introduction of new polymer blends that enhance the strength, flexibility, and UV resistance of molded products is shaping the market. These materials are designed to meet specific industry needs, such as more durable outdoor furniture and robust industrial containers.
- Automation in Manufacturing: Automation technology is being integrated into the rotational molding process to increase efficiency and reduce labor costs. Automated molding machines that ensure consistent quality and faster production cycles are becoming more prevalent, appealing to manufacturers looking to scale operations.
- Customization and Complexity: There’s a growing demand for custom and complex mold designs that can be achieved through rotational molding. Manufacturers are leveraging this capability to offer bespoke solutions to customers, particularly in sectors like bespoke furniture and specialized automotive components.
- Expansion in Developing Markets: As emerging economies continue to grow, the demand for cost-effective manufacturing solutions like rotational molding is increasing. This trend is driving the expansion of the market into new regions, opening up fresh opportunities for growth in areas such as Asia and Africa.
Use Cases
- Water Storage Tanks: Rotational molding is extensively used to produce large, durable water storage tanks. These tanks are valued for their seamless construction and long-lasting material properties, making them ideal for residential, agricultural, and industrial water storage applications.
- Outdoor Furniture: This technique is perfect for creating outdoor furniture due to its ability to mold complex shapes and incorporate vibrant colors that are UV resistant. The resulting products offer both aesthetic appeal and high durability against weather elements.
- Automotive Components: Rotational molding materials are used to make various automotive parts, including dashboards, fuel tanks, and storage bins. The method provides a cost-effective solution for producing hollow, lightweight parts that contribute to the overall efficiency and performance of vehicles.
- Playground Equipment: The safety and durability requirements of playground equipment make rotational molding a preferred manufacturing method. It allows for the creation of large, sturdy pieces with smooth surfaces to ensure child safety.
- Shipping Containers: The industry relies on rotational molding to produce rugged shipping containers designed to withstand the rigors of transport and handling. These containers can be custom-made to fit various dimensions and specifications, proving essential for logistics and storage solutions.
Major Challenges
- High Production Times: One of the main challenges with rotational molding is the longer cycle times compared to other molding methods like injection molding. This can limit production efficiency and increase operational costs, especially for high-volume manufacturing needs.
- Limited Material Options: While advancements are being made, the range of materials suitable for rotational molding is still somewhat limited compared to other processes. This restricts the application in industries requiring materials with specific properties, such as high temperature or chemical resistance.
- Quality Consistency: Achieving consistent quality can be challenging in rotational molding due to variables like temperature control and timing. Inconsistencies in these factors can lead to defects in the final product, such as uneven thickness or weak spots.
- Environmental Impact: The process typically uses polyethylene and other plastics, which raises concerns about environmental sustainability. The industry faces pressure to find eco-friendly materials and practices to reduce its carbon footprint and dependence on fossil-based resources.
- Technical Skill Requirements: Rotational molding requires a high level of technical expertise to manage the intricate parameters of the molding process. There is a growing need for skilled workers, and the lack of trained professionals can hinder the operational capacity of manufacturing facilities.
Market Growth Opportunities
- Expansion into New Markets: There’s a significant opportunity for growth by expanding into emerging markets, particularly in Asia and Africa, where industrial and consumer product demands are increasing. Local manufacturing facilities could be established to capitalize on lower production costs and growing market needs.
- Development of Advanced Materials: Innovating new polymer blends that enhance the properties of rotationally molded products, such as improved impact resistance and UV stability, could open up new applications in sectors like aerospace and automotive.
- Eco-Friendly Solutions: There is a growing demand for sustainable manufacturing processes and materials. Developing recyclable or biodegradable rotational molding materials could attract new customers and comply with global environmental regulations, creating a competitive advantage.
- Customization Capabilities: Leveraging the unique ability of rotational molding to easily create complex and custom shapes can attract niche markets and specialty product manufacturers, offering them tailored solutions not feasible with other molding techniques.
- Technological Integration: Implementing advanced automation and IoT (Internet of Things) technologies in the rotational molding process can increase production efficiency, reduce costs, and improve product quality, thus enhancing market competitiveness and appeal.
Recent Developments
1. SCG Chemicals
- SCG Chemicals has been focusing on sustainability and circular economy initiatives. The company announced partnerships to develop advanced recycling technologies for plastic waste, aiming to produce high-quality rotational molding materials.
2. LyondellBasell Industries Holdings B.V.
- LyondellBasell has been expanding its portfolio of sustainable polymers, including materials suitable for rotational molding. The company launched CirculenRecover, a product line made from mechanically recycled plastics.
3. ExxonMobil
- ExxonMobil has been investing in advanced recycling technologies to produce high-performance polyethylene resins, which are used in rotational molding applications. The company announced a new facility in Texas to expand its polymer production capacity.
4. Reliance Industries Limited
- Reliance Industries has been actively working on expanding its polymer and petrochemical business, including materials for rotational molding. The company announced a new plant in Gujarat, India, to produce specialty polymers.
5. SABIC
- SABIC has been focusing on developing sustainable materials for rotational molding. The company introduced a new line of bio-based polyolefins, which are designed to reduce carbon footprint.
Conclusion
The Rotational Molding Materials Market is poised for significant growth, driven by its flexibility in creating complex and durable products across various industries. As the market continues to expand into new regions and adopts innovative materials, the development opportunities are vast. By focusing on sustainability, technological advancements, and customization, companies can address the challenges and meet the increasing demand for efficient and environmentally friendly products.
Discuss Your Needs With Our Analyst
Please share your requirements with more details so our analyst can check if they can solve your problem(s)
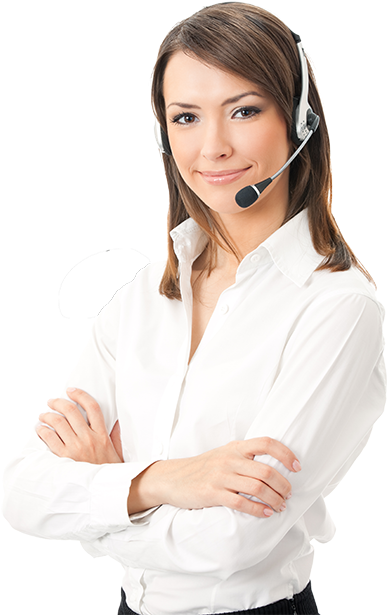