Table of Contents
Overview
New York, NY – May 26, 2025 – The Global Oil and Gas Corrosion Protection Market is set to grow significantly, driven by increasing demand for durable and cost-effective solutions to protect infrastructure. The market, valued at USD 9.4 billion in 2024, is projected to reach USD 13.5 billion by 2034, expanding at a CAGR of 3.7%.
In 2024, Coatings captured 48.3% of the market share. Widely used on pipelines, tanks, and offshore structures, coatings offer cost-effective, versatile protection against moisture, salinity, and extreme temperatures, ensuring durability and preventing corrosion-related damage in harsh oil and gas environments.
Offshore Environments held a 67.7% market share in 2024, driven by exposure to saltwater and humidity. The Upstream sector accounted for 49.3% of the market. Exposure to corrosive substances like hydrogen sulfide drives demand for coatings and inhibitors, preventing equipment failure and costly downtime in exploration and production activities.
US Tariff Impact on Oil and Gas Corrosion Protection Market
On March 4, 2025, the Trump Administration imposed tariffs of 10% on Canadian and 25% on Mexican oil and gas imports, paused until April 2, 2025, per President Trump’s March 6 announcement. Canada and Mexico, supplying 70% of U.S. crude oil imports in 2022 (mostly from Canada) and 99% of natural gas imports (almost entirely from Canada via pipeline), are critical energy partners.
Despite the U.S. being the world’s top oil producer, its refineries, designed for heavier crude, rely on Canadian imports, as most domestic crude is lighter. The tariffs are estimated to cost USD 6.5 billion annually (USD 5.2 billion from Canada, USD 1.3 billion from Mexico), with effective tax rates of 7.1% for Canada and 14.1% for Mexico.
➤ Get More Detailed Insights about US Tariff Impact @ – https://market.us/report/global-oil-and-gas-corrosion-protection-market/request-sample/
These tariffs will likely raise gasoline prices by 20–30 cents per gallon in the short term, increase refining costs, and pass higher prices to consumers. Additionally, proposed 25% tariffs on steel imports, announced for March 12, could raise U.S. oil well construction and maintenance costs by 3.25%, due to reliance on imported steel for drilling equipment, further straining the oil and gas industry.
Key Takeaways
- Global Oil and Gas Corrosion Protection Market is expected to be worth around USD 13.5 billion by 2034, up from USD 9.4 billion in 2024, and grow at a CAGR of 3.7% from 2025 to 2034.
- In 2024, Coatings held a 48.3% share by type in the Oil and Gas Corrosion Protection Market.
- Offshore installations dominated with 67.7% market share by location in corrosion protection applications for oil and gas.
- The upstream sector accounted for a 49.3% share, leading demand in Oil and Gas Corrosion Protection solutions.
- Corrosion protection demand in the Middle East and Africa captured a 34.7% market value.
Report Scope
Market Value (2024) | USD 9.4 Billion |
Forecast Revenue (2034) | USD 13.5 Billion |
CAGR (2025-2034) | 3.7% |
Segments Covered | By Type (Coatings, Paints, Corrosion Inhibitors, Others), By Location (Offshore, Onshore), By Sector (Upstream, Midstream, Downstream) |
Competitive Landscape | 3M Company, Akzo Nobel N.V., Ashland Global Specialty Chemicals Inc., Axalta Coating Systems Ltd., BASF SE, Chase Corporation, Cortec Corporation, Hempel A/S, Hexigone Inhibitors Ltd., Imperial Oilfield Chemicals Pvt. Ltd., Jotun A/S, Maxwell Additives Pvt. Ltd., Metal Coatings Corp., RPM International Inc., SLB (Schlumberger Limited), Teknos (Teknos Group), The Sherwin-Williams Company |
➤ Directly purchase a copy of the report – https://market.us/purchase-report/?report_id=147806
Key Market Segments
By Type Analysis
- Coatings’ Market Leadership: In 2024, coatings captured 48.3% of the market share. Widely used on pipelines, tanks, and offshore structures, coatings offer cost-effective, versatile protection against moisture, salinity, and extreme temperatures, ensuring durability and preventing corrosion-related damage in harsh oil and gas environments.
- Broad Applicability of Coatings: Coatings are favored for their ease of application and compatibility with various surfaces. They protect critical assets like valves and pipelines, reducing maintenance costs and ensuring long-term performance in demanding upstream and offshore operations.
By Location Analysis
- Offshore’s Dominant Share: Offshore environments held a 67.7% market share in 2024, driven by exposure to saltwater and humidity. Robust corrosion protection for platforms and subsea pipelines ensures safety, minimizes costly repairs, and maintains efficiency in challenging marine conditions.
- Offshore Asset Protection: Harsh marine conditions accelerate corrosion, making advanced coatings and cathodic systems vital for offshore rigs and pipelines. These solutions reduce downtime and protect expensive infrastructure, supporting reliable operations in remote locations.
By Sector Analysis
- Upstream’s Leading Role: In 2024, the upstream sector accounted for 49.3% of the market. Exposure to corrosive substances like hydrogen sulfide drives demand for coatings and inhibitors, preventing equipment failure and costly downtime in exploration and production activities.
- Upstream Infrastructure Needs: Upstream operations face high-pressure, chemically aggressive environments. Protective coatings and advanced materials ensure well integrity and operational continuity, addressing the sector’s extensive global infrastructure and maintenance challenges.
Regional Analysis
- The Middle East and Africa emerged as the dominant regional market, accounting for 34.7% of the global share with a value of USD 3.2 billion. Steady demand stems from mature upstream operations and aging asset maintenance. Corrosion protection solutions extend infrastructure life, ensuring safety and efficiency across North America’s oil and gas facilities.
- Strict safety and integrity regulations fuel Europe’s corrosion protection demand. Coatings and systems ensure compliance, protecting assets from environmental wear and supporting reliable operations across the region. Rising energy needs in emerging economies drive corrosion protection use in refineries and offshore platforms. Solutions safeguard assets against harsh conditions, ensuring operational efficiency and infrastructure durability.
- Focused on Brazil’s offshore fields, Latin America’s market is smaller. Corrosion protection solutions counter marine degradation, supporting reliable production and minimizing maintenance costs in challenging environments. Regions like the Middle East face extreme conditions, necessitating advanced corrosion protection. Coatings and cathodic systems ensure asset longevity and safety in high-exposure oilfield infrastructure.
Top Use Cases
- Offshore Platform Protection: Corrosion protection coatings and cathodic systems shield offshore platforms from harsh marine conditions like saltwater and humidity. These solutions prevent metal degradation, ensuring safety and extending platform lifespan, reducing costly repairs and downtime in remote locations.
- Pipeline Integrity Maintenance: Protective coatings and inhibitors safeguard pipelines from corrosion caused by crude oil, gas, and environmental factors. This ensures leak-free transport, minimizes environmental risks, and maintains operational efficiency across long distances.
- Storage Tank Durability: Anti-corrosive coatings and linings protect storage tanks from chemical reactions with stored oil or gas. This extends tank life, prevents leaks, and reduces maintenance costs, ensuring safe storage and regulatory compliance.
- Drilling Equipment Protection: Corrosion inhibitors and coatings shield drilling rigs and equipment from harsh substances like hydrogen sulfide. This prevents equipment failure, enhances safety, and supports uninterrupted upstream exploration and production activities.
- Refinery Asset Longevity: Advanced coatings and cathodic protection systems protect refinery infrastructure from high temperatures and corrosive chemicals. This ensures operational continuity, reduces downtime, and supports cost-effective maintenance in downstream processes.
Recent Developments
1. 3M Company
- 3M has introduced advanced corrosion-resistant coatings and pipeline tapes for oil and gas applications. Their Scotchkote Polyurethane Coatings provide long-term protection against harsh environments. Additionally, 3M’s corrosion protection solutions now incorporate smart monitoring technologies to predict coating failures. These innovations help extend asset life in offshore and onshore operations.
2. Akzo Nobel N.V.
- Akzo Nobel’s International Paint brand launched Interzone 954, a high-performance coating for offshore oil and gas structures. The product offers enhanced corrosion resistance under extreme conditions. The company also focuses on sustainable anti-corrosion solutions, reducing VOC emissions while maintaining durability.
3. Ashland Global Specialty Chemicals Inc.
- Ashland has developed high-temperature-resistant coatings for oil and gas pipelines. Their Sculptural and Aroset epoxy systems provide superior adhesion and chemical resistance. Recent advancements include self-healing coatings that automatically repair minor damages, improving asset longevity.
4. Axalta Coating Systems Ltd.
- Axalta’s Nap-Gard M coating system is gaining traction in oil and gas for its high dielectric strength and corrosion protection. The company also introduced fast-curing coatings to reduce downtime in pipeline maintenance. Their IoT-enabled coatings help monitor corrosion in real-time.
5. BASF SE
- BASF has expanded its CathoGuard 800 cathodic protection coatings for subsea pipelines. Their smart coatings integrate sensors for real-time corrosion monitoring. BASF also collaborates with oil majors to develop eco-friendly corrosion inhibitors for sour gas environments.
Conclusion
The Oil and Gas Corrosion Protection Market is poised for steady growth, driven by the increasing need to safeguard aging infrastructure and comply with stricter environmental regulations. Demand for advanced coatings, inhibitors, and cathodic protection systems remains strong. The expansion of offshore drilling, shale gas production, and pipeline networks further boosts opportunities, particularly in fast-growing regions like Asia-Pacific and the Middle East. Innovations such as smart coatings, self-healing materials, and IoT-based corrosion monitoring are transforming the industry, offering more efficient and long-lasting solutions.
Discuss Your Needs With Our Analyst
Please share your requirements with more details so our analyst can check if they can solve your problem(s)
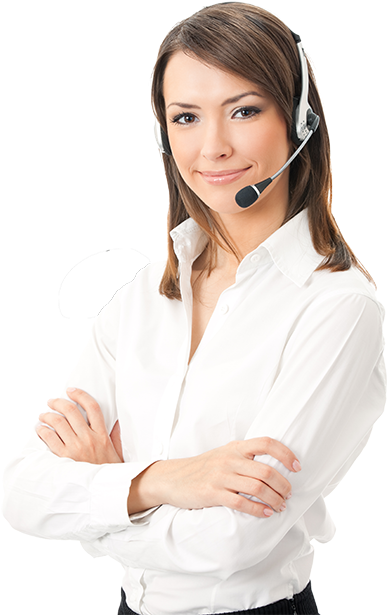